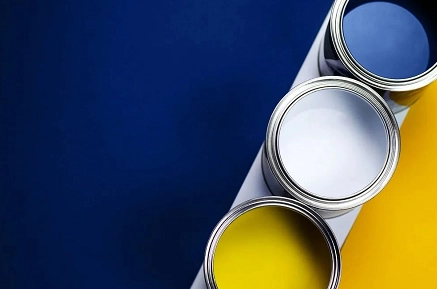
The leveling of the coating film is the embodiment of the apparent performance of the coating. The leveling of the coating involves many aspects, such as viscosity, rheology of the coating, matching of raw materials, pigment dispersion, selection of additives, coating process and environment. and other factors.The leveling of the paint generally requires the addition of a suitable leveling agent. Different types of leveling agents have different mechanisms of action and different effects. Even if the types of leveling agents are the same but have different structures, the use effects are also different. Therefore, when applying leveling agents, it is necessary to choose according to the problems that the coating needs to overcome and the structural category of the additives. When applying, it is necessary to pay attention to the matching of leveling agents and other additives, their negative effects and overcoming methods. This article briefly describes the role of leveling agents in coatings.
-
Anti-shrinkage cavity.
The shrinkage cavity on the surface of the coating film is one of the common problems. The cause of the shrinkage cavity is the imbalance of surface tension. The substance that produces shrinkage cavities must have a lower surface tension than the coating film, and is called a shrinkage cavity donor. The surface tension of the coating film must be higher than that of the shrinkage cavity donor, which is called the shrinkage cavity acceptor. The reasons can be summarized as follows.
1. When several kinds of resins are blended together, when the solvent is properly matched, they can be compatible with each other and even form a transparent coating film. However, when the solvent is mixed improperly, some resins will be precipitated during the solvent volatilization process, and the colloidal particles will become shrinkage cavity donors.
2. Pollution from external objects, low surface energy floating objects in the air, silica gel particles in the drying tunnel, etc. fall on the surface of the coating film; the coating contains low surface energy substances such as insoluble oil, silicone oil, colloidal particles and other materials.
3. The surface tension of the substrate is unbalanced, some places are polluted by substances with low surface energy or the surface energy of the substrate is too low.
4. Add substrate wetting agent to paints containing pigments or matt powders that have not been treated with wetting and dispersing agents. At this time, the substrate wetting agent will be adsorbed to the exposed particle surface, and shrinkage cavity donor will be formed. . Such disadvantages often occur in water-based matt paints.
-
Anti-orange peel, anti-color fading, prevent extinction, light leakage and fading.
1. The root cause of these disadvantages is that the surface tension of the surface layer and the lower layer of the solvent evaporation coating is unbalanced, the lower layer is lower, and the upper layer is higher; in addition, the density of the surface layer is greater than that of the lower layer. The underlying solvent-rich paint is pushed toward the surface by surface tension, and gravity causes the top paint to sink, creating a vortex motion of sinking, expanding, and rising. The result is an irregular mesh of hexagons where the edges meet. Call it a “Bernar” vortex. The low surface tension of fresh, solvent-rich paint in the center of the grid pushes it toward the edges, where it accumulates to form a hillock, which is orange peel. This movement can also result in differences in color and pigment content. This is the main reason for the blooming of the color paint and the uneven distribution of the sub-powder of the matte paint, which causes light leakage and matting. The Marangoni movement is the main source of these disadvantages. As long as the surface tension of the coating film is reduced, the underlying paint cannot be pushed to the surface, and the above-mentioned disadvantages cannot be produced. Therefore, adding those that can control the surface state and reduce the surface tension, silicone leveling agents are commonly used additives.
2. Prevent ripples. The generation of corrugation is also caused by the uneven surface tension, but we should pay attention to whether it is vertical spraying or flat spraying. When spraying on a flat surface, the drying speed of the coating film is uneven, and the surface tension of the fast-drying area is higher than that of the slow-drying area. At this time, the surface tension will push the paint in the slow-drying area to move toward the fast-drying area, resulting in ripples in the left and right directions. This can be solved with a silicone-based leveling agent that lowers the surface tension. However, when the vertical spraying produces up and down ripples, it is best not to use a leveling agent that reduces the surface tension to solve it, otherwise it will become more and more serious. This is because the paint is falling, and the surface tension below is higher than that above, so the paint is pushed from bottom to top, and gravity sinks, which produces up and down ripples. The more the leveling agent that reduces the surface tension is added, the lower the surface tension will be, the stronger the upward force will be, and the stronger the ripple will be. A common solution is to add a leveling agent that does not lower the surface tension.