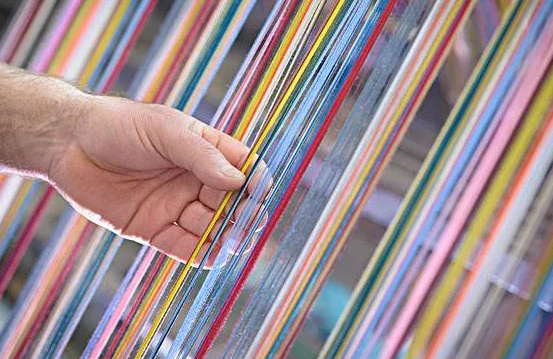
Application of powder coating in textile printing and dyeing
Powder coating does not use water or solvent as the dispersing medium, but with the help of air as the dispersing medium. Therefore, basically, there are no three wastes, no pollution, energy saving, safe to use, high utilization rate, and can obtain the equivalent effect with the use performance of liquid paint.
01、Application
The coating has no affinity to the fiber, it dissolves in the medium and is completely bonded to the fiber with the help of polymer binder. After baking at high temperature, the binder forms a wear-resistant transparent resin film with certain elasticity on the surface of the fabric, and the coating particles in the film layer adhere to the fiber.
Coating can be used for fabric dyeing, for example, cotton / dimensional blended fine cloth with firm, breathable, comfortable and warm, cheap and other excellent features, but cotton / dimensional fabric disadvantages are poor color, wrinkle resistance and ease of dyeing poor, in the color after the phenomenon of silver silk clip flowers. For this reason, it is greatly restricted in dyeing.
The method of dyeing with paint is that the fabric is pre-treated first, and dyed after drying wool, desizing, boiling, chlorine bleaching, pickling, open rolling and drying, and mercerizing.
Its dyeing process is simple, the dip dyeing solution will be pre-drying, hot drying, far-infrared baking, stentering, finished products after the installation of Juan that is completed.
With the coating can replace the reactive dyes on dyeing pure cotton and instead of reducing dyes to produce pure cotton, etc. Its can alleviate the shortage of dyeing and chemical materials, and less material, low cost, energy saving, energy saving, environmental pollution, good economic and social benefits.
(1) A formula of dyeing solution: powder coating Xg, binder 8g, cross-linking agent Yg, emulsifying paste 1g, ping ping plus O 2g, penetrating agent JFC 1g/L.
(2) Formulation for cotton/virgin orange red fine flat cloth dyeing: powder coating orange red FGRN 3g, binder 8g, emulsifying paste 1g, ping pong O 2g, penetrating agent 1g/L.
(3) For cotton/vegetable green fine flat cloth dyeing formula: powder coating emerald green F4G 5g, binder 12 g, emulsifying paste A 1.5g, ping ping plus O 2g, penetrating agent 1g/L.
Powder coating is generally non-toxic, good chemical stability resistance, strong adhesion, excellent physical properties, and is the most promising product in coating production.
02、Production process
There are various methods of powder coating production, such as dry mixing method, melt extrusion mixing method, precipitation method, evaporation method, spray drying method, etc.
Usually there are two preparation methods, one method is to add various additives to the resin, after dry mixing, melt mixing, selection of grains deep cold crushing to get finished products; another method is to mix the formula materials in a high-speed mixer heating sieving system.
2.1 PVC powder coating
100 parts of PVC resin, 30 parts of DOP, 2 parts of dibutyltin dilaurate, 2 parts of dibutyltin thiol, 5 parts of pigment.
Add the above materials into the mixer, heat and mix at 120℃, cool down and make PVC powder coating.
2.2 Acrylic resin powder coating
1%~100% colloidal acrylic resin-polyester [hydroxyl value 10~100mg KOH/ g, softening point (S-P) 50~150 ℃], 0%~90% polyester [hydroxyl value 10~100, (S-P) 50~150 ℃], 0%~90% acrylic resin [hydroxyl value 30~50, (S-P) 50~150 ℃], 5~50 parts of polyisocyanate.
Produced by hybridization method, i.e., using high-curing polyester resin hybridized with acrylic resin, the resin used has high color-carrying power, which can solve the most difficult color matching problem in the process.
The production process is as follows: 150 parts of methyl methacrylate, 30 parts of butyl acrylate, 90 parts of hydroxyethyl methacrylate and 30 parts of styrene are used for polymerization.
Then in toluene solvent with 92 parts of terephthalic acid, 15 parts of isophthalic acid, 5 parts of glycolic acid, 8 parts of maleic anhydride, 30 parts of ethylene glycol, 100 parts of neonjonediol and 5 parts of trimethylolpropane to make high solids acrylic resin coating.
2.3 Epoxy-polyester powder coating
The basic component of this powder coating is dry thermoplastic or thermosetting resin, and the particle diameter of polymer is 3 ~ 30μm.
Make 1 part of 57% styrene solution (containing 44 parts of 3 I 1 I 45 parts of maleic anhydride-phthalic anhydride-1. 2-propanediol copolymer) with TiO2 3.5 parts, MgO 0.18 parts, styrene 20 parts and water 4.9 parts after the reaction 1 1, then slowly add 42 parts of water and emulsifier, then vulcanize, flocculate and dry into a sphere.
2.4 Polyester powder coating
Made with 50:25:25 (mol) of 1. 4-butanediol-maleic anhydride terephthalic acid copolymer 100 parts, hydrogenated polybutadiene-maleic anhydride crosslink 5 parts, TiO2 100 parts and talc 0.5 parts mixed in a high-speed mixer, mixed and sieved.
2.5 Acrylic-polyester powder coating
Polymerized with 150 parts of methyl methacrylate, 30 parts of butyl acrylate, 90 parts of hydroxyethyl methacrylate and 30 parts of styrene.
The polymer containing 700 parts of polyester is made from 72 parts of terephthalic acid, 15 parts of isophthalic acid, 5 parts of glycolic acid, 8 parts of maleic anhydride, 30 parts of ethylene glycol, 100 parts of neonjonediol and 5 mol of trimethylolpropane in xylene solvent.
The mixture of 100 parts, 43 parts of polyisocyanate, 40 parts of TiO2 and leveling agent are mixed, cooled and granulated to obtain powder coating.
03、Conclusion
Powder coating can be made into various colors as needed, and has excellent impact resistance and flexibility, and the surface is flat and smooth after coating and baking on the metal surface.
With the application of thin coating film and new technology, the weather resistance of coating film will be improved. The market of powder coating lies in the continuous introduction of new products to ensure that the products have good repeatability, and its development prospects will be better.