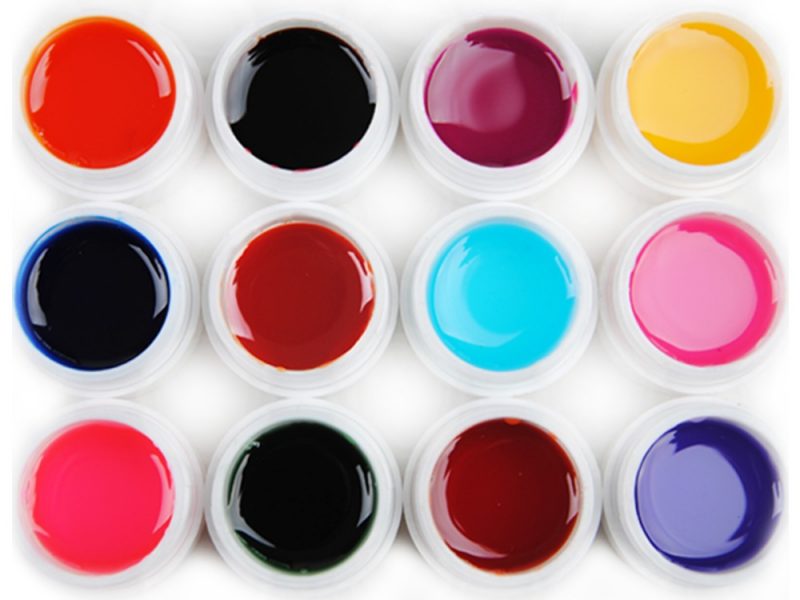
Application of alicyclic epoxy resins in UV light curing coatings
UV cationic and UV free radical materials are very different, but the overall composition is similar. Cationic system is mainly epoxy materials, but the ordinary bisphenol A type epoxy reaction speed is slow, with more applications of alicyclic epoxy / oxetane type materials; free radical system commercialization is now very mature, to epoxy / polyester / polyurethane modified acrylate materials can provide more choice of solutions.
The UV cationic system has fewer raw materials than the free radical system, and the low viscosity alicyclic epoxy resin is the main polymer. Take alicyclic epoxy resins as an example.
TTA21 of various purity specifications is the most dominant product in the UV coating industry. As the application of cationic UV coatings continues to grow significantly, it is expected that the amount of alicyclic epoxy resins represented by TTA21 will increase.
Performance Differences
In the specific product application of ink/coatings, in addition to the fact that both require UV light to provide curing energy, the two systems exhibit major differences in performance and reaction characteristics.
1. Oxygen blocking effect
UV cationic system does not have the effect of oxygen barrier, but more afraid of water, moisture will affect the curing efficiency of the cationic system; UV free radicals, on the contrary, are more affected by oxygen barrier.
2. Substrate adhesion
Usually in the more difficult to adhere to the surface of the substrate, such as glass / metal / high-density plastic, UV cation than UV free base has better adhesion performance.
3. Volume shrinkage rate
UV free radical system formulations generally curing shrinkage rate of 10% or more, while UV cationic system can control the shrinkage rate of 1-3%, is a good solution to solve the volume shrinkage.
4. Dark curing characteristics
UV cation system can continue to react to the inner layer after stopping the light source irradiation, to complete the material after curing, this is the dark curing characteristics, very suitable for thick coating applications, heating the cation after curing speed is significantly helpful; UV free radical is a stop-and-go reaction system.
5. Contact safety
UV cation system reaction degree is close to 100%, safety can be REACH / FDA testing certification, can be used in food packaging and other related fields.
6. Light curing speed
In general UV free radical system curing speed than the cationic system to be faster, affected by the oxygen barrier products cationic surface drying will be faster, but the actual drying speed is not as fast as the free radical, can be heated to promote the reaction, and ultimately can reach a very good degree of completion.
Recipe Notes
UV cation system can be mixed with UV radical system in any proportion, known as UV hybrid system, can improve the UV cation relative curing speed and UV radical shrinkage, affected by oxygen blocking and other shortcomings, the same film thickness of the system curing energy difference is not large.
UV cation system is to rely on the initiator generated by Lewis strong acid to do the active point of the ring-opening reaction, the formula will commonly affect the initiator activity of the material is mainly azo organic pigments (can be modified to do protection), and free radicals mixed with TPO/819/907 and other structures containing P, S and other elements of the initiator, and similar to 115 multi-level amine.
Humidity has a greater impact on the UV cation system curing, control the ambient humidity within 50% is appropriate; while heating will speed up the reaction rate.