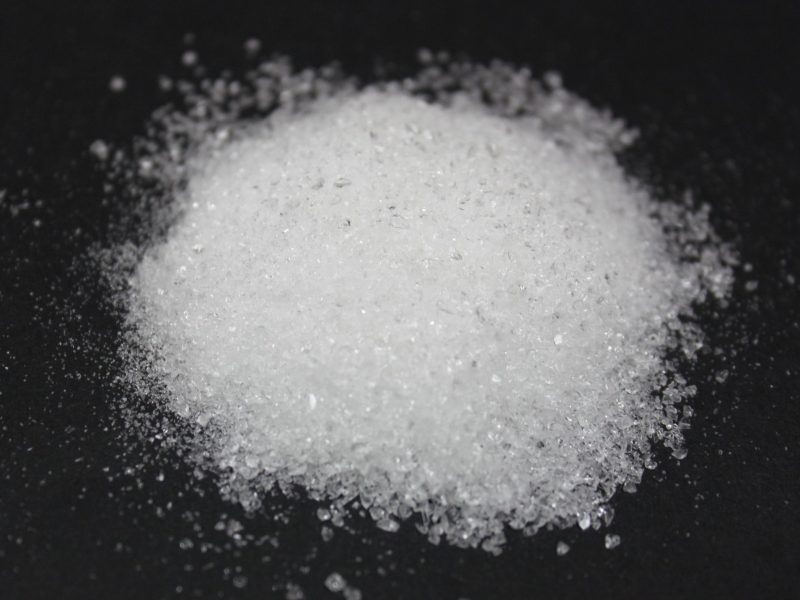
How to select light stabilizer?
Light stabilizers as a polymer products (such as plastics, rubber, coatings, synthetic fibers) additives, can shield light, absorb and transfer light energy, burst or capture free radicals, so that polymers in the light radiation can exclude or slow down the possibility of photochemical reactions, to prevent or delay the process of light aging, so as to achieve the purpose of extending the service life of polymer products.
Light stabilizers are generally divided into four categories: light shielding agents, UV absorbers, bursting agents and hindered amine light stabilizers according to the mechanism of action.
Hindered amine light stabilizer (HALS) is a class of organic amine compounds with spatial site resistance effect, because of its decomposition of hydrogen peroxide, burst excited state oxygen, capture free radicals, and the effective group can be recycled and regenerated, is the largest amount of a class of light stabilizers at home and abroad. Domestic consumption of hindered amine light stabilizers account for about 65% of the total consumption of domestic light stabilizers.
UV-absorbing light stabilizers are commonly known as UV absorbers, these light stabilizers are the use of their own molecular structure, the conversion of light energy into heat, to avoid photo-oxidation of plastic materials and play a role in light stabilization. UV absorbers are divided into benzophenones and benzotriazoles according to their molecular structure. Domestic consumption of benzophenone and benzotriazole light stabilizers account for about 25% and 10% of the total consumption of domestic light stabilizers, respectively.
Bursting agents and UV absorbers are light stabilizers through the transfer of light energy to achieve the purpose of light stabilization. UV absorber is its own molecules directly absorb light energy when transferring energy, burst is with the plastic due to light and high energy, high chemical reactivity of the excited state functional groups to interact with the transfer of the energy of the excited state functional.
It is because of the burst and UV absorbers transfer energy mechanism is completely different, burst is listed as one of the four series of light stabilizers. The industrial product of bursting agent is a complex of divalent nickel, its molecules contain heavy metal nickel, from the protection of the environment and human health considerations, Europe, North America and Japan and other developed countries and regions have stopped or limit the use of bursting. Domestic burst production plant is only one.
Light shielding agents are carbon black, titanium dioxide, zinc oxide, etc. The industrial application of nanotechnology will substantially improve the light shielding agent in the plastic material light and weather resistance performance.
Domestic light shielding agent, ultraviolet absorber, bursting agent three types of light stabilizers in the 1960s before and after the industrial application, and hindered amine light stabilizer, although the mid-1970s before the industrial production, but its product variety and production rate of increase is much higher than the other three types of stabilizers, is a plastic light stabilizer family of rising stars.
What is the principle of selecting light stabilizers?
Mainly based on the type and model of plastic materials, processing equipment and process conditions, the variety of other chemical additives and the amount added, the use of the product environment and the duration of a comprehensive determination of factors. The selection of light stabilizers for industrial use should basically refer to the following principles.
(1) compatibility. Plastic polymer polymer is very polar, while the light stabilizer molecules have different degrees of polarity, the two are less compatible, usually at high temperatures to light stabilizer and polymer melt bonding, polymer curing will be light stabilizer molecules compatible in the middle of the polymer molecules. In the formulation dosage range, the light stabilizer to melt at the processing temperature, pay special attention to the design of the formulation, the choice of light stabilizer melting point or the upper limit of the melting range, should not be lower than the processing temperature of plastic polymers.
It has been proved that the amorphous phase at the interface of the polymer crystal area spherical crystal, is the most susceptible to oxidation in the polymer matrix, solubility is good just concentrated in the region where they are most needed in the polymer.
(2) Mobility. Plastic products, especially the surface area to volume ratio (or mass ratio) value of small products, oxidation occurs mainly on the surface of the product, which requires continuous migration of light stabilizers from the interior of the plastic product to the surface of the product and play a role.
However, if the migration rate to the surface of the product is too fast, the migration amount is too large, the light stabilizer should be volatile to the product surface of the environment, or diffusers and other media contact with the product surface and loss, this loss is in fact unavoidable, the design of the formulation to consider. When there is a choice of light stabilizer varieties, should choose a relatively large molecular weight, melting point appropriate higher varieties, and to the most severe use of the environment to determine the amount of light stabilizer use.
(3) Stabilizer. Light stabilizer in the plastic material should remain stable, in the use of the environment and high temperature processing process volatile loss less, no discoloration or color, not decomposition (except for processing heat stabilization effect), not adverse chemical reaction with other additives, not corrosive machinery and equipment, not easy to be extracted by other substances on the surface of the product. Hindered amine light stabilizer is generally low alkaline products, plastic materials selected hindered amine for light stabilizer, the formula should not contain acidic other additives, the corresponding plastic products can not be used in acidic environments.
(4) processability. Plastic products processing, the addition of light stabilizers on the resin viscosity and screw torque may change. Light stabilizer on the resin melting range if the difference is large, will produce light stabilizer bias flow or inhibition of screw phenomenon. When the melting point of the light stabilizer is lower than the processing temperature of 100 ℃ or more, the light stabilizer should be made into a certain master batch first, and then mixed with resin processing products, in order to avoid uneven distribution of light stabilizer in products and processing yield decline due to bias flow.
(5) Environmental and health. Light stabilizer should be non-toxic or low toxicity, no dust or low dust, no harmful effects on humans in the processing and use of plastic products, no harm to animals and plants, no pollution of air, soil and water systems.
For agricultural film food packaging boxes, children’s toys, disposable infusions and other indirect or direct contact with food, drugs, medical devices in contact with the human body in plastic products, should not only be selected through the U.S. Food and Drug Administration (FDA) inspection and permission, or the European Commission decree allows the light stabilizer species, and the amount added should be strictly controlled within the maximum allowable limit.