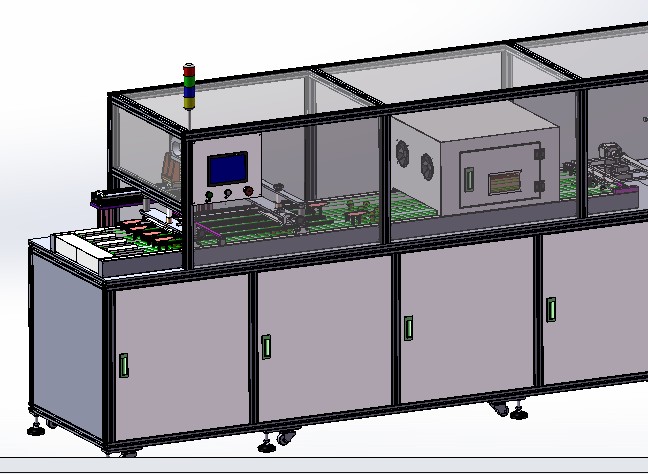
Is your UV curing system not working as it should? Are you constantly replacing overheated lamps? Maintaining a healthy UV curing system is critical to achieving successful curing results and saving money by reducing unplanned downtime due to poorly maintained UV equipment. There are five elements to building a healthy UV curing system:
A suitable lamp cooling system with adequate air flow;
power maintenance;
proper light shielding;
reflector maintenance;
Lighting maintenance.
Paying close attention to each of the above factors can solve problems that may have persisted in your UV curing process, or can avoid problems with the curing effect of your equipment. The five elements discussed here apply to both arc UV systems and microwave (electrodeless) UV lamp systems.
Cooling and Airflow
Maintaining proper air cooling is critical to the healthy functioning of almost any UV curing lamp system. UV lamps operate at very high temperatures (approximately 800°C/1,500°F on the bulb surface) to maintain a consistent and complete mercury plasma state inside the UV lamp.
More advanced UV lamp systems require a cooling system that not only maintains lamp stability within this range, but also protects the integrity of the metal structure of the lamp during operation. The most common way to cool a UV lamp is to flow air through its housing, UV lamp and reflector. However, to ensure consistent UV output and long UV lamp life, there are a few things to consider when designing your UV lamp air cooling system.
To achieve proper air cooling, UV lamps do have a “cooling window”. It is possible for the cooling process to over-cool or under-cool. To complicate matters, the amount of cooling air required to be sent through the UV lamp will depend on the operating power level of the UV lamp.
Most current UV lamp systems are powered by variable power ballasts, which range in power from 20% to 100%. Such a wide power adjustment range will allow the lamp to vary from 130 watts/inch to 650 watts/inch. For some UV systems, the power setting is adjusted from the front control panel, but for more complex UV systems, lamp power is automatically adjusted based on line speed via a customer-supplied signal of 0 to 10VDC or 4 to 20mA .
As the power of the lamp goes up, it needs more cooling air to pass through the UV lamp to prevent overheating. Conversely, when the lamp power is reduced, the cooling air must be reduced to ensure that the lamp does not get too cold. Therefore, in order to avoid lamp cooling problems, the cooling system must be able to automatically adjust to match the lamp power and thermal load, thereby maintaining lamp stability and ensuring that it operates within its proper temperature range.
Operating the lamp in overheated conditions can shorten its life and may cause the lamp to expand or distort, adversely affecting the UV output.
Operating the lamp in supercooled conditions can also result in shorter lamp life and lower UV output. When the lamp is too cold, it cannot produce the correct voltage and maintains a very high current (Amperes), and in this condition for a long time, the electrodes will suffer from undesirable wear. In most cases, when the lamp gets too cold, the mercury plasma will start to become unstable and the lamp may suddenly go out.
Maximum UV lamp life and consistent UV lamp output can only be achieved when the lamp operates continuously within the correct cooling parameters.
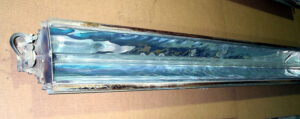
Figure 1. Insufficient lamp cooling. Overheating of the lamp can cause twisting and wrinkling of the reflector, as well as sagging of the UV tube into a banana shape, reducing the UV radiation output
Another critical part is the condition and performance of the reflector, which in any UV system requires good maintenance to ensure the healthy operation of the curing system. The reflector, usually semi-elliptical or parabolic, surrounds the upper half of the bulb and covers the entire length of the working UV lamp.
Figure 1 shows an overheated reflector. Lamp reflectors are an important part of a UV lamp system because they are typically responsible for reflecting approximately 65% of the UV light energy emitted by the bulb onto the customer’s product, as shown in Figure 2. If the reflector is not properly cooled, it may warp and wrinkle due to thermal expansion. A reflector that loses its curved shape diffuses or scatters the light reflected off the customer’s product, which negatively affects its ability to cure.
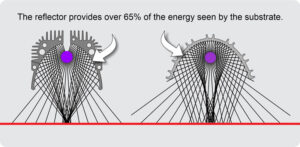
Figure 2. These two traditional light modes are used in most UV curing systems. The reflector provides more than 65% of the radiant energy emitted by the UV lamp to the customer’s product
Figure 2 illustrates the two conventional light-gathering modes used in most UV curing systems. It is critical that the curved shape of the reflector does not change during lamp operation in order to maintain the focusing pattern of these UV rays. The curved shape of the reflector is often designed to concentrate (or focus) light into a small area, resulting in extremely high peak UV irradiance on the customer’s product, which is one of the key points of UV curing.
In addition to maintaining the desired reflector surface, routine maintenance of the reflector is also very important. During use, when the reflector becomes dirty, polluted or dull, the light reflectivity is greatly reduced, which in turn reduces the UV energy and intensity delivered to the product.
Poor reflector condition will result in product not fully cured. The reflector is considered a consumable part of all UV systems and requires attention and maintenance (or regular cleaning) to help ensure consistent UV light output from the lamp system.
Some UV systems use a replaceable reflector liner, which is usually made of a thin polished aluminum material with a protective coating (looks a lot like traditional mirror paint), and is usually pre-curved and cut to fit the installation in the reflector holder inside the lamp housing.
Some UV lamps use a “cold mirror” reflector. They are also thin, pre-bent and cut aluminum or glass reflectors that fit into the internal brackets of a particular type of lamp holder. Chilled mirror reflectors have a special coating on the reflective surface. The coating is designed to reflect UV light effectively, but absorbs the infrared energy (heat) emitted by UV lamps. Chilled mirror reflectors will reduce the heat experienced by customer products as they pass under UV lamps.
Less sophisticated UV systems use a polished aluminum extrusion as a reflector that curves around the UV lamp and acts as a reflector and light switch shade.
Regardless of the reflector type, it is important to keep the reflector in a clean, shiny appearance. If the mirror starts to look dull or dirty, it needs to be cleaned or replaced.
The reflector can be cleaned with a lint-free cloth and isopropyl alcohol, or with a surface cleaner that does not leave a film. Ammonia-based cleaners are not recommended.
If the reflector still appears dull or dirty after cleaning, it should be replaced. In almost all cases, a dirty or dull reflector can have a greater impact on the reduction in UV output than an old or underperforming UV lamp.
Measuring the UV output will also help determine if the reflector is underperforming. The best device for measuring UV output is a “disc” radiometer, which measures the energy of UV light in all four UV wavelength ranges: UVA, UVB, UVC, and UVV. Disc radiometers are placed on a conveyor belt and run under a UV lamp at a preset constant speed. It will measure the total UV light energy emitted by the lamp. When the UV light energy is reduced to a point where proper curing may not be possible, it is likely that the lampshade reflector will need to be cleaned and/or replaced.
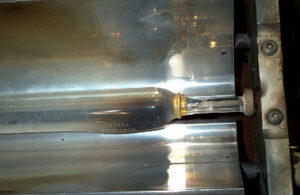
Figure 3. Dirty, overheated lamps can bend and expand at both ends, greatly reducing UV output energy and lamp life expectancy.
Routine maintenance of lamps is also key to maintaining a healthy UV curing system. Most UV lamps typically operate in industrial environments that are less than ideal. It is important to keep the lamp as clean as possible to help ensure consistent UV output and prolong its lifespan. Lamps that are neglected will suffer from low UV output energy, rapid aging, and premature failure.
The easiest way to keep UV lamps clean is to clean them with a designated UV glass bulb cleaner and a lint-free cloth. The frequency of UV lamp cleaning varies according to the environment in which they are operated.
Dirty and contaminated UV lamps under extended operating conditions are more likely to overheat and then expand or warp (Figure 3). If the UV lamp expands or warps, it will negatively affect the UV peak irradiance of the lamp, as well as the curing performance of the system. Once the UV lamp becomes swollen or deformed, it should be replaced.
If air filters are used to keep the lamp cooling air clean (as is common practice in microwave UV lamp systems), these filters will need to be replaced periodically to ensure cooling delivered into the housing and through the UV lamp (and reflector) The air is clean. Maintaining a clean air filter also helps ensure that the amount of air delivered to the lamp remains within the required range. If the air filter of the UV lamp system is dirty, clogging can occur, which almost always causes the UV lamp to overheat and greatly reduces the life of the UV lamp.
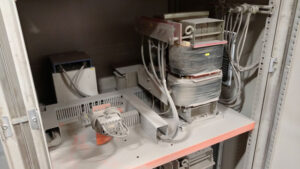
Figure 4 Dirty ballasts and internal electrical components will overheat the power supply and shorten the life of these components
Let’s move on to another factor important to maintaining a healthy UV curing system: power maintenance.
At the heart of any UV curing system is the expensive power supply that drives the UV lamps. Whether traditional iron core ballasts or solid state power units are used, the appropriate amount of filtered cooling air delivered to the ballast is critical to the health and life expectancy of any ballast and other electrical components within the ballast assembly housing. Critical.
Power supplies operating in dirty or overheated environments will prematurely age or even fail, resulting in lower UV output energy or loss of capacity. Maintaining a clean air filter and proper air flow to the ballast ensures that the ballast is properly cooled and kept clean. Depending on the actual usage environment, the air filter should be replaced as often as necessary. If the ballast and other internal power components (such as capacitors) are covered with dust or dirt (as shown in Figure 4), it is strongly recommended that you do both of the following:
- Check the air filter and replace if necessary.
2. Blow out the ballast and all other internal components with clean, dry compressed air, then vacuum to remove any settling dust.
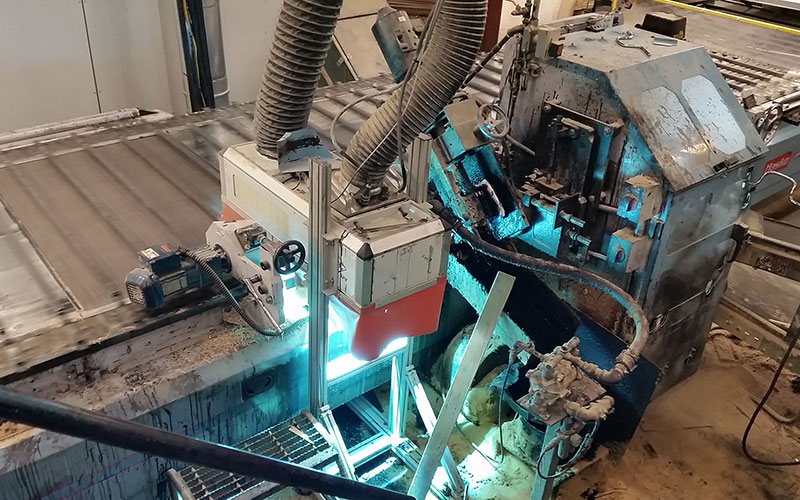
Figure 5 Poor UV shielding can lead to harmful UV exposure to personnel near UV equipment
The final factor in maintaining a healthy UV curing system involves light shielding. The main purpose of light shielding is to protect personnel from any direct exposure to UV light (Figure 5).
Good shielding in and around the UV lamp housing will protect the lamp module assembly and the production machines that install it. A properly designed hood will effectively prevent any machine hardware near the UV lamp from reaching unsafe temperatures or accelerated aging due to direct exposure to UV light.
The secondary function of the hood is to effectively support the UV lampshade, so that the product can be effectively cured. If the hood is removed from the machine for equipment maintenance, it must be reinstalled in the same location and orientation to ensure the UV lamp is placed in the correct location and orientation.
The third function of the hood is to contribute to good air cooling. Some hoods may have air intakes or louvers to allow air to enter the interior of the hood for lamp cooling, substrate cooling, and/or hood cooling. If the air intake is clogged with dust or dirt, it can cause the UV lamp, hood and substrate to heat up. The result can be poor UV lamp performance, shorter lamp life or overheating of customer substrates. Regular brush and vacuum cleaning of the air intake holes (or shutters) on the hood, or dry compressed air, should be part of a routine preventive maintenance program.
in conclusion
Five key elements to maintaining a healthy UV curing system include: proper lamp air cooling, power maintenance, proper light shielding, maintaining good reflector conditions, and performing routine lamp maintenance. Keeping the system in a healthy state improves machine performance, reduces downtime, maintains personnel safety, and achieves proper curing results.