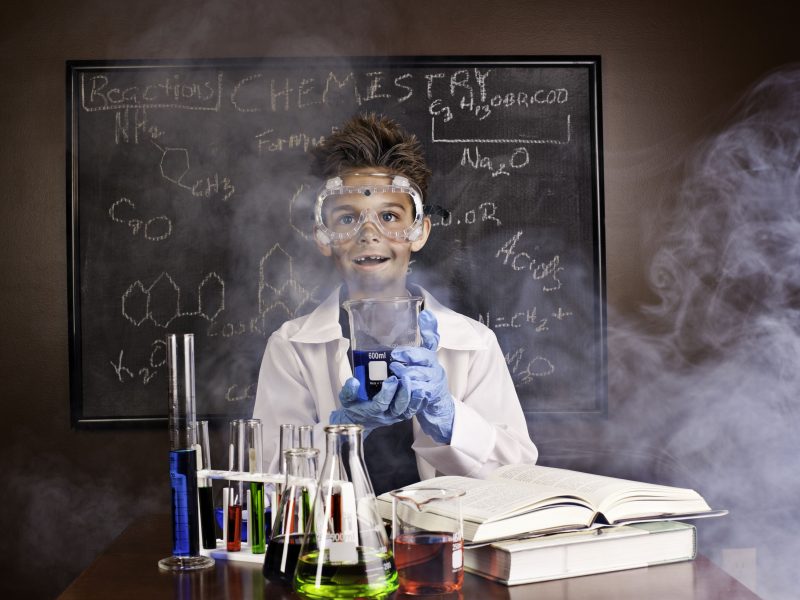
If there are two or more ways to do something,and one of those ways can result in a catastrophe,then someone will do it.
Every accident is actually inevitable. In every accident, there is carelessness and fluke mentality behind it.
On March 21, 2019, Jiangsu Xiangshui Tianjiayi Chemical Co., Ltd.’s long-term illegal storage of nitrification waste continued to heat up, causing spontaneous combustion, burning and exploding, causing 78 deaths, 76 serious injuries, 640 hospitalizations, and direct economic loss 19,863.07. Ten thousand yuan.
On September 2, 2011, two graduate students from East China University of Science and Technology were accidentally injured by an explosion when they were doing a chemical experiment. Their bodies and faces were injured by the splashed glass debris. They needed surgery to remove the glass debris that penetrated into the skin. The reason is that when the two of them were doing the oxidation reaction experiment, they added hydrogen peroxide, ethanol and other chemical materials too quickly, and they did not pull down the fume hood door as required and did not wear personal protective equipment.
On December 29, 2008, at the University of California, Los Angeles, a female student of the school was unfortunately ignited by spilled chemicals while doing tert-butyl lithium reaction in the laboratory, and was unable to use the emergency field device in the first time. She was not wearing protective clothing, causing severe burns all over her body and died.
In fact, most of the accidents in laboratories and chemical plants are not unforeseen and inevitable accidents, but are caused by negligence or overconfidence and the lack of a complete and strict safety management system. There is more or less inertness in everyone’s heart. During experiments and production, they often fail to take protective measures to avoid trouble, and the lack of protective measures eventually leads to tragedies. The author hopes that through this article, more people can raise their awareness of laboratory safety and avoid more tragedies.
How to avoid these tragedies? The author believes that the following aspects should be considered:
First, build a complete laboratory safety management system. Complete laboratory safety management regulations should be formulated to investigate, warn and avoid all possible dangers, including at least the following aspects:
(1) Standards for the labeling, management, storage and use of explosives, precursors, and highly toxic chemicals. For example, volatile organic solvents, strong acids and bases, toxic reagents and corrosive reagents should be operated in a fume hood, and the ventilation should be opened and the cabinet door should be pulled down; reagents should be classified and stored, and reagents that are likely to react with each other should be separated store.
(2) Specifications for special laboratory equipment and electrical safety and fire protection. Different types of fires use different methods of extinguishing fire. Wrong extinguishing methods can sometimes promote the spread of fire. It is necessary to strengthen the fire fighting training for operators, understand what kind of fire corresponds to which fire fighting method, and be proficient in operating fire extinguishers.
(3) Safety management and standardized disposal of laboratory waste. Avoid incorrect classification and handling, causing environmental pollution and harm to sanitation workers.
(4) Regulations for the protection of laboratory personnel. For example: when performing operations with toxic and corrosive reagents, the requirements for wearing protective gloves, protective glasses, protective masks, gas masks, and protective clothing; long hair should be tied up during the experiment, and no slippers, etc. should be worn.
(5) Laboratory safety operation specifications. For example, during experiment operation, it is strictly forbidden to point the mouth of the bottle to people; avoid conducting dangerous experiments alone.
(6) Emergency handling and demonstration of safety accidents of dangerous goods in the laboratory.
(7) Ensure that experimenters can strictly abide by the management system of the safety management standard, for example, through mutual supervision, rewards and punishments, notifications, etc.
Second, carry out pre-job safety training. In fact, the most important thing in training newcomers is not to teach experimental skills, but to teach experimental safety. If the concept of safe operation cannot be transmitted from the very beginning, it is difficult to avoid illegal operations in future experimental operations, which will eventually lead to tragedies. Once heard of a very strange thing, a student was operating a high-performance liquid chromatograph and the pipe got air bubbles. He had no sense of safe operation at that time, so he directly pointed his mouth at the pipe filled with organic solvents. The bubbles of the solvent are sucked out of the pipe. Fortunately, the amount sucked in is small and there is no poisoning.
Third, establish risk identification, assessment, control and emergency response mechanisms. The existing laboratory safety management regulations cannot completely list all the hazards. The experimenters and managers should dig out and discover potential safety hazards or safety incidents that may exist in the laboratory, and evaluate the hazard levels and causes of the risks. And the possibility, targeted preventive measures, and emergency measures in case of occurrence.
For example, it is found that people often do not turn off the instrument in time after the experiment is done at night, causing the instrument to run for a long time without being supervised, which may lead to serious loss of the instrument, and even more serious risk of fire. In response to this situation, you can take turns to arrange personnel to conduct safety inspections in the laboratory after the night experiment is completed, and when it is found that the instrument is not turned off, or the instrument is malfunctioning, after calling the operator, take measures to close it. , And record the situation in the safety inspection logbook.
Finally, share with you some details and solutions that may be overlooked in the experiment:
(1) Treatment of broken glass. If the broken glass is thrown into the trash can, it may hurt the hands of the cleaner who handles the trash. Solution: You can consider wrapping the broken glass before throwing it away, or throwing it into a cardboard box that collects broken glass for separate treatment.
(2) Glove protection when contacting organic reagents. Experimenters usually only wear a layer of rubber gloves when they come into contact with organic reagents, but the rubber gloves may be dissolved and penetrated by organic solvents, and absorbed by the skin. Solution: You can add another layer of PE gloves that can resist organic solvents to the rubber gloves.
(3) Pay attention to the use of sharp instruments. When using a syringe with a needle to transfer solvent, the needle may be pierced into the skin and the solvent may be penetrated into the body, which may cause serious damage. Solution: Use flat needles instead of sharp needles.
(4) Attention to the use of ultrasound equipment. Prolonged exposure to ultrasound can cause hearing loss. Solution: Cover or physically isolate to reduce noise; stay away.
(5) Cleaning of containers with organic and toxic reagents. If the containers containing organic and toxic reagents are cleaned directly after being poured, the cleaning staff will inhale the volatilized residual reagents, which may cause serious damage, and the residual solvents will be discharged into the sewer and pollute the environment. Solution: After cleaning the container with water three times in a fume hood, perform ultrasonic cleaning, and pour the waste liquid into the waste liquid bucket.