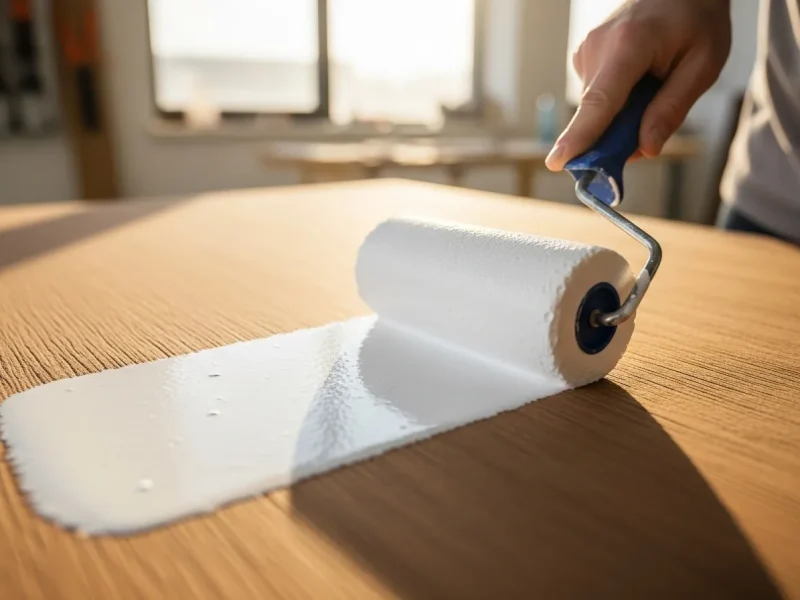
How Silicone Defoamers Optimize Industrial Production
The Persistent Challenge of Industrial Foam
In countless manufacturing and chemical processes, the formation of foam is a persistent and costly issue. It can reduce equipment capacity, decrease production efficiency, and even compromise the quality of the final product. The solution requires a specialized chemical additive, and among the most effective is the silicone defoamer. This advanced organosilicon compound is engineered to eliminate and suppress foam with remarkable efficiency. Due to its unique chemical structure based on siloxane, it works effectively even at extremely low concentrations. Furthermore, its stability in harsh environments—including high temperatures, extreme pressures, and both strong acid and alkali conditions—makes it an indispensable tool for technical applications.
Critical Applications in Textiles and Petrochemicals
The versatility of silicone defoamers is best illustrated by their widespread use in demanding sectors like textiles and petrochemicals. In the textile industry, controlling foam is crucial at nearly every stage. During the sizing process, for example, adding a water-emulsion silicone defoamer prevents bubbles that could lead to uneven yarn coating. For dyeing processes, especially high-temperature jet dyeing, a polyether-modified silicone defoamer is ideal because it maintains its antifoaming properties at high heat while remaining water-soluble at lower temperatures, ensuring no residue is left on the fabric.
In the petrochemical industry, the applications are equally critical. From oil drilling to refining, foam control directly impacts output and safety.
- Drilling and Extraction: Silicone-based additives are mixed into drilling mud to prevent foam that can interfere with equipment. In oil extraction, defoaming rods or additives help separate gas from crude oil more effectively.
- Refining: During vacuum distillation, adding a silicone defoamer can improve the color and broaden the range of distilled fractions.
- Lubricants: These defoamers are added to lubricants for internal combustion engines and metalworking fluids. Their low solubility in oil allows them to remain dispersed and effectively rupture air bubbles as they form, preserving the lubricant’s integrity.
For more details on our specific product formulations, you can [explore our chemical additives page].
Enhancing Production in Paper, Coatings, and Inks
Foam presents a significant obstacle in the manufacturing of paper and coatings, where a smooth, uniform finish is paramount. Silicone defoamers provide a reliable solution. In the papermaking process, a silicone emulsion defoamer added during the pulping stage can significantly reduce entrained air, leading to a stronger, higher-quality paper sheet. Similarly, they are used in wastewater treatment within paper mills to manage foam buildup.
The requirements for coatings and inks are particularly stringent. A defoamer must not only break down bubbles but also be compatible with the coating system to prevent surface defects like “fish eyes” or craters in the final dried film.
- Water-Based Coatings: Modified silicone resins are often the best choice for aqueous systems, as they have low surface tension and are insoluble in water, allowing them to effectively migrate to the bubble surface.
- Non-Aqueous Coatings: For solvent-based systems, different formulations are used, but the principle remains the same. A precise dosage is crucial, as too much defoamer can cause its own set of surface imperfections.
Specialized Uses in Detergents and Food Processing
Beyond heavy industry, silicone antifoaming agents are formulated for specialized applications, including consumer products and food manufacturing. In powdered detergents, silicone defoamers are often combined with other chemicals and added to the formula to control suds during the wash cycle, improving cleaning efficiency, particularly in front-loading washing machines. For industrial metal cleaning fluids that operate under highly alkaline conditions, specially designed silicone defoamers maintain transparency and activity.
In the food industry, food-grade silicone defoamers—primarily composed of dimethylpolysiloxane—are used to control foam during the processing of products like fruit juices, jams, and cooking oils. These additives are strictly regulated to ensure consumer safety and are highly effective at preventing boil-over and ensuring consistent production.
The Clear Choice for Superior Foam Control
From initial processing to the final product, uncontrolled foam can hinder productivity and compromise quality across a vast range of industries. Silicone defoamers provide a powerful, reliable, and cost-effective solution. Their ability to perform under extreme conditions, combined with their effectiveness at very low concentrations, makes them a superior choice for any technical end-customer looking to optimize their operations. By selecting the correct type of silicone antifoaming agent for a specific application, companies can ensure smoother production runs, higher-quality outputs, and a more efficient process overall.
Ready to eliminate foam and enhance your production efficiency? For more information, technical support, or to receive a quote on the right silicone defoamer for your needs, please send us an email at info@sinocurechem.com. Our team of experts is ready to assist you.