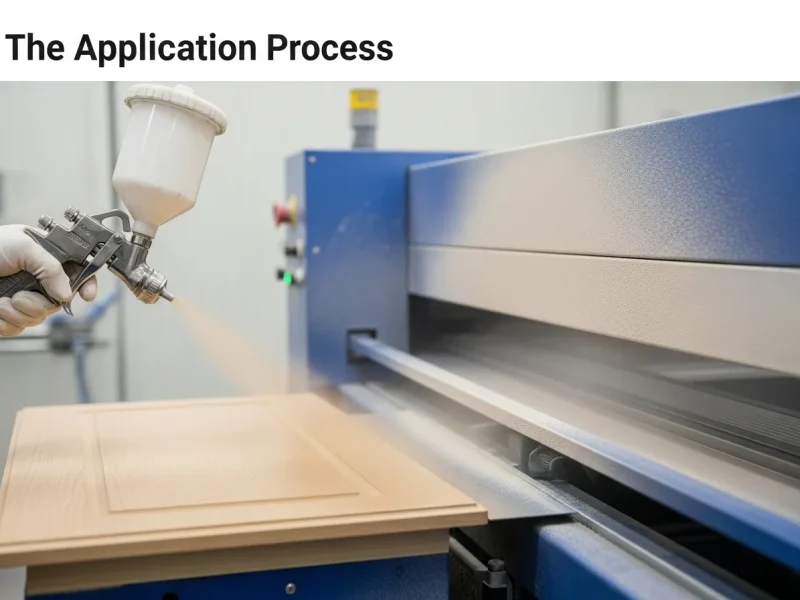
A Complete Guide to Water-Based Coating Formulation Components
The Complex Chemistry Behind Modern Coatings
As industries move away from traditional solvent-based paints, water-based coatings have become the new standard for performance, safety, and environmental compliance. However, these systems are far more than just pigment and water. A successful water-based coating formulation is a complex, finely-tuned system where every component has a critical role. Unlike their solvent-borne counterparts, water-based systems require a sophisticated balance of additives to manage everything from stability in the can to the final film’s performance. Understanding these components is the first step toward achieving a flawless, durable finish for any application.
Core Components: The Foundation of Your Coating
Every coating builds upon a foundation of essential ingredients that determine its fundamental properties. In a water-based system, these core components are responsible for creating the protective film and ensuring it forms correctly.
- Water-Based Resin: This is the binder and the heart of the coating. The choice of resin (e.g., acrylic, polyurethane, epoxy) dictates the final film’s primary characteristics, such as hardness, flexibility, chemical resistance, and adhesion.
- Film-Forming Aids (Coalescents): As water evaporates during the drying process, these solvents temporarily soften the resin particles, allowing them to fuse (coalesce) into a continuous, uniform film. This is especially crucial for achieving optimal performance in low-temperature applications.
- Deionized Water: The primary carrier and diluent in the formula. Using deionized water is critical to prevent unwanted reactions with salts or minerals that could destabilize the formulation.
Functional Additives: Controlling Behavior and Application
While core components form the film, functional additives control how the coating behaves during manufacturing, storage, and application. They are the problem-solvers that ensure a stable, easy-to-use product. Key functional coating additives include:
- Surfactants (Wetting Agents & Dispersants): These are crucial for integrating pigments and fillers into the water-based system. Wetting agents reduce surface tension, allowing the coating to properly wet the substrate, which improves adhesion and flow. Dispersants ensure that solid particles are evenly distributed and do not clump together.
- Defoamers and Deaerators: Air bubbles can become trapped during mixing and application, leading to surface defects like pinholes. Defoamers prevent foam from forming and help release any entrapped air.
- Rheology Modifiers (Thickeners): These control the coating’s viscosity. They provide good flow and leveling during application while preventing sagging on vertical surfaces. For pigmented coatings, they are also vital for preventing pigments and fillers from settling during storage.
- pH Adjusters: Maintaining a stable pH is critical for the longevity and consistency of the emulsion. These additives, often amines, prevent the formulation from breaking down.
- Preservatives & Biocides: Because they are water-based, these coatings can be susceptible to microbial growth. Preservatives are added to prevent spoilage and ensure a long shelf life.
Performance Additives: Tailoring the Final Finish
Once the coating is stable and applicable, special-purpose additives are used to enhance the final properties of the dried film. These components deliver the specific performance characteristics a technical end-customer demands.
- Colorants and Fillers: Pigments and dyes provide color and opacity, while fillers can increase the coating’s solids content, improve sandability, and reduce cost.
- Wax Emulsions & Powders: These additives migrate to the surface of the film as it dries, improving scratch resistance, mar resistance, and modifying the tactile feel (hand-feel).
- Matting Agents: For applications requiring a low-gloss finish, agents like silica or waxes are used to scatter reflected light, reducing sheen.
- Crosslinkers: Used to create two-component (2K) systems, crosslinkers react with the resin to create a much tougher, more chemically resistant film suitable for high-demand applications.
- Specialty Additives: This category is vast and includes everything from UV absorbers for exterior durability to anti-blocking agents that prevent coated surfaces from sticking together when stacked.
Achieving Excellence Through Balanced Formulation
A high-performance water-based coating is far more than its base resin. It is a carefully engineered system where each ingredient, from wetting agents to wax emulsions, plays a synergistic role. Achieving the desired outcome—whether it’s superior hardness, a specific gloss level, or outdoor durability—depends entirely on a well-designed and balanced water-based coating formulation. By understanding the function of each component, formulators can troubleshoot issues, optimize performance, and create products that meet the highest technical standards.
For more information, technical support, or to receive a quote on our coating additives, please send us an email at info@sinocurechem.com. Our team of specialists is ready to assist you.