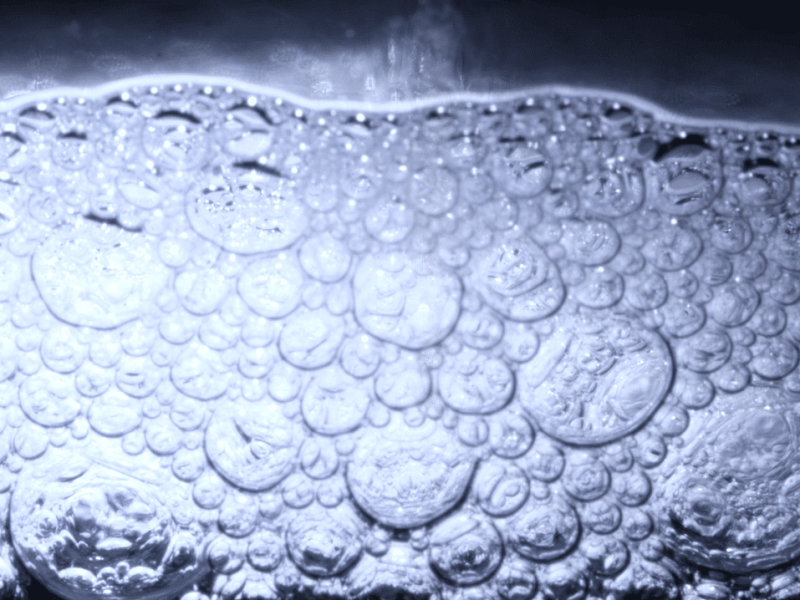
Unveiling the Power of Silicone Defoamers: Enhancing Efficiency Across Industries
In countless industrial processes, from manufacturing life-saving pharmaceuticals to producing everyday consumer goods, an unwelcome guest often makes an appearance: foam. While seemingly innocuous, uncontrolled foam can lead to a cascade of problems, including reduced production efficiency, equipment damage, safety hazards, and compromised product quality. But what if there was a highly effective and versatile solution? Enter the silicone defoamer, a specialized chemical additive designed to combat and control problematic foam, ensuring smoother and more reliable operations. This article delves into the diverse application areas of silicone defoamers, highlighting why they are indispensable in modern manufacturing.
Silicone defoamers, primarily composed of siloxane-based compounds, are renowned for their superior antifoaming mechanism. They work by reducing surface tension at the liquid-air interface, causing foam bubbles to destabilize and collapse. Even in remarkably low concentrations, these powerful agents effectively eliminate existing foam and prevent its recurrence. Their remarkable stability allows them to perform exceptionally well even in challenging high temperature/high pressure/acidic and alkaline environments. Furthermore, a key advantage is their environmentally friendly and reliable nature, ensuring they don’t introduce harmful pollutants. These characteristics make them a preferred choice over some mineral oil substitutes or older non-silicone antifoam agents.
The Science Behind the Solution: How Silicone Defoamers Work
At its core, a silicone defoamer operates due to its unique chemical structure. Silicones, or siloxane-based compounds, have very low surface tension. When introduced into a foaming system, the defoamer spreads rapidly across the surface of the foam bubbles. This action, often described by its HLB value (hydrophilic-lipophilic balance), displaces the stabilizing surfactants in the foam lamella (the thin liquid film of the bubble). As the silicone defoamer spreads, it creates a lens on the bubble surface that thins and eventually ruptures the bubble wall. This rapid spreading and destabilization is key to their efficiency. Think of it like a tiny, targeted disruption that brings a chaotic foamy sea back to a calm, manageable state.
According to a 2023 industry report on process efficiency, uncontrolled foaming can lead to a decrease in output by as much as 15% in certain chemical processing plants, underscoring the economic necessity of effective foam control. Silicone defoamers address this head-on, often requiring minimal antifoam agent addition amounts to achieve desired results.
Core Application Areas of Silicone Defoamers
The versatility of silicone defoamers is evident in their widespread use across numerous sectors. Let’s explore some of the primary application areas:
1. Textile Printing and Dyeing: Ensuring Quality from Start to Finish
The textile printing and dyeing industry heavily relies on wet processing, where foam generation is a common challenge. Silicone defoamers play a crucial role in several stages:
- Sizing Process: Water emulsion-type defoamers, such as those based on polyether silicone, are added to sizing baths (e.g., 0.2-0.25g/L) to prevent foam that can lead to uneven sizing application and yarn breakage.
- Fiber Oil Agents: Incorporating a water emulsion type silicone defoamer (0.02-0.04%) into fiber oil formulations, which often contain silicone oil, ensures smooth application and prevents processing issues.
- Desizing and Scouring: Polyether silicone defoamers are selected for their effectiveness in these preparatory stages, removing sizes and impurities without problematic foam.
- Bleaching: In highly acidic bleaching environments, the robust nature of silicone defoamers makes them ideal for controlling foam.
- Dyeing: Silicone defoamer emulsions are standard. For jet dyeing processes, polyether silicone is preferred due to its excellent high-temperature defoaming capabilities and low-temperature water solubility, preventing fabric staining.
2. Petrochemical Industry: Optimizing Complex Processes
The petrochemical industry, with its intricate refining and processing operations, faces significant foam-related challenges that can impede efficiency and safety. Silicone defoamers are critical:
- Drilling: Ethyl silicone oil or methyl silicone oil emulsions are used as mud additives to control foam during drilling operations.
- Oil Extraction: Defoaming sticks, often utilizing silicones with melting points 2.8-13.9°C above wellhead foam temperature, are employed for oil-gas separation.
- Natural Gasoline Absorption: A 2% solution of dimethylsilicone oil in gasoline helps manage foam.
- Oil-Gas Separation & Demulsification:
- Adding a mere 0.025–0.0065mg/Kg of silicone defoamer to crude oil can significantly enhance production capacity during separation.
- For W/O (water-in-oil) emulsions common in separated crude, approximately 0.2mg/Kg of a suitable silicone defoamer achieves both demulsification and defoaming.
- Refining: Adding silicone defoamers during vacuum distillation improves distillate color and widens the fraction range. Diesel solutions of silicone oil are commonly used.
- High-Energy Fuels: Cyanocene polysiloxanes dispersed in high-flashpoint kerosene serve as highly effective defoamers in internal combustion, jet, and aviation fuels.
- Asphalt and Residual Oil: Silicone oil addition amounts range from 0.2×10⁻⁶ to 2.0×10⁻⁶.
- Delayed Coking, Decoking, Descaling: Reference addition rates for silicone defoamers are 0.05–100×10⁻⁶.
- Defoaming Drilling Fluids: High-viscosity sulfonated metal salts (e.g., calcium petroleum sulfonate: sulfonated asphalt sodium = 1:1) are combined with siloxanes (approx. 100–400×10⁻⁶ or 5–15mg/Kg), ideally with a sulfonate to siloxane ratio close to 1:1.
- Lubricants: Silicone defoamers are added to engine oils, automotive lubricants, metalworking fluids, and compressor oils due to their insolubility (remaining dispersed to act on bubbles), alkyl groups similar to mineral oil (allowing them to penetrate foam films), and low surface tension (causing uneven surface tension and bubble rupture). For heavy oils, low-viscosity silicone oil is used at 1–10×10⁻⁶.
3. Paper Industry: Smooth Production from Pulp to Paper
In the paper industry, foam can disrupt nearly every stage of production. Silicone defoamers ensure a smoother flow:
- Pulping: Silicone defoamer emulsions (e.g., 90g/tonne of paper) are used to control foam generated during the pulping process, preventing deposits and ensuring consistent pulp quality.
- Coated Paper: While non-silicone antifoam agents are often used for coating formulations to avoid surface defects like fisheyes, careful selection and application of modified silicones can be beneficial.
- Wastewater Treatment: Water emulsion-type silicone defoamers are crucial in treating the large volumes of wastewater generated, preventing foam from hindering the efficiency of treatment processes. Effective wastewater treatment is a significant concern, and silicones help manage this sustainably.
4. Coatings and Inks: Achieving Flawless Finishes
For coatings and inks, foam is detrimental to the final appearance and protective qualities. Silicone defoamers must meet specific requirements:
-
General Requirements for Coatings:
- Affinity for foam-stabilizing surfactants but insoluble in the foaming liquid.
- Surface tension lower than the foaming liquid, with a low HLB value.
- Must maintain emulsion (latex) stability.
- Crucially, must not cause “fisheyes” or “craters” (shrinkage and fisheye control) in the dried film.
- Water-based coatings: Often use water-insoluble substances like mineral oils, higher alcohols, and silicone resins. Organic silicones are generally considered the best for these systems.
- Non-aqueous coatings: Employ substances poorly soluble in organic solvents, like lower alcohols or silicone resins (used judiciously to prevent defects; modified or emulsified silicone resins are preferred).
-
Recommended Silicone Defoamers for Water-Based Coatings:
- Silicone oil/hydrophobic SiO₂ mixtures: Suitable for epoxy resins (casting, 0.3% usage), thermoplastic acrylic resins (spraying, 0.3%).
- Polyether polysiloxane/hydrophobic SiO₂ mixtures: Ideal for thermosetting alkyd resins (dip coating 0.3%, knife coating 0.1%).
- Hydrophobic SiO₂/hydrocarbon/silicone oil mixtures: Used in thermoplastic acrylic resins for printing inks (0.1%), air-drying acrylic resins (casting, 0.5%).
- Silicone oil/hydrophobic SiO₂ mixture emulsions: Applied in alkyd-modified styrene-acrylic resins (casting, 0.5%).
5. Detergent Industry: Enhancing Cleaning Power
Even in the detergent industry, where some foam might be desired for consumer perception, excessive or persistent foam can be problematic in automatic washing machines or industrial cleaning processes.
- Polysiloxanes and modified trisodium phosphate are used as additives in powder detergents. Dimethylsilicone oil (1500c.s) emulsions containing 2-6% SiO₂ are mixed with anhydrous trisodium phosphate (emulsion usage 10-40%) to form a hydrate additive.
- For metal cleaning solutions, alkali resistance is key. The defoamer should ideally be transparent when added to liquid products and maintain its antifoaming activity. Some formulations even look for flame retardant properties depending on the application.
6. Food Industry: Safety and Purity First
In the food industry, foam control is essential for hygiene, process efficiency, and product quality. Only specially approved food-grade antifoam agents can be used.
- Food-specific polysiloxane resins, primarily dimethylpolysiloxane with less than 15% SiO₂, are employed. If the food product is an aqueous solution, an emulsified version of the defoamer is used. For other applications, oil-type products can be directly applied, with strict control over the antifoam agent addition amount. These agents act as emulsion stabilizers in some contexts and are critical for applications like fermentation, beverage production, and dairy processing. Could you imagine a jam factory constantly battling overflows or a brewery struggling with inconsistent fermentation due to foam? Food-grade silicone defoamers prevent these issues.
Why Choose Silicone Defoamers? The Decisive Advantages
The widespread adoption of silicone defoamers isn’t accidental. They offer a compelling package of benefits:
- High Efficiency: Effective at very low concentrations.
- Versatility: Perform well across a wide pH range and temperature spectrum.
- Persistence: Provide long-lasting foam control.
- Chemical Inertness: Generally do not react with the processed materials.
- Ease of Use: Available in various forms (emulsions, oils, powders) for easy incorporation.
- Environmental Profile: Many formulations are environmentally friendly and reliable, contributing to sustainable manufacturing.
- Cost-Effectiveness: Low dosage rates and prevention of foam-related losses lead to overall savings.
Studies in chemical engineering have shown that the implementation of an optimized defoaming strategy using silicone defoamers can increase the throughput of a distillation column by up to 10-20% by preventing foaming entrainment, directly impacting profitability.
Making the Right Choice for Your Application
While silicone defoamers offer numerous advantages, selecting the correct type and dosage is crucial for optimal performance and to avoid issues like shrinkage and fisheye control in coatings. Factors such as the nature of the foaming medium, temperature, pH, agitation, and regulatory requirements (e.g., food-grade antifoam) all play a role.
The journey to effective foam control begins with understanding your specific needs. Are you dealing with a water-based system or an oil-based one? Is high temperature a concern? Do you require a food-grade antifoam?
Partner with Us for Your Foam Control Solutions
Navigating the world of chemical additives can be complex. If you’re facing challenges with foam in your processes or are unsure which silicone defoamer is right for your application areas – from textile printing and dyeing and the petrochemical industry to the paper industry, coatings and inks, detergent industry, or food industry – we are here to help.
Our team of experts can provide guidance on product selection, optimal antifoam agent addition amounts, and troubleshooting. Don’t let foam hinder your productivity or compromise your product quality.
Ready to eliminate foam and enhance your operational efficiency? Send us an inquiry today to discuss your specific needs and discover the ideal silicone defoamer solution! If you have any questions or need further clarification, please don’t hesitate to consult with us.