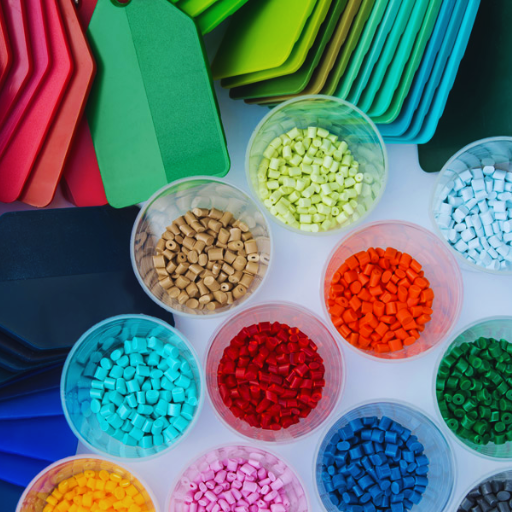
Plasticizers: Unlocking Flexibility and Performance in Polymers
Ever wondered how some plastics are incredibly rigid while others are surprisingly supple and bendable? The secret often lies in a crucial group of additives known as plasticizers. These unsung heroes of the material world are indispensable in transforming the properties of polymers, making them more versatile for a vast array of industrial applications. From the flexible insulation on electrical cables to the soft texture of children’s toys and the durability of automotive interiors, plasticizers play a pivotal role.
This guide will delve into the world of plasticizers, exploring their essential functions, the main components that define their characteristics, and the exciting developments in environmentally friendly plasticizers. Understanding these aspects is key for anyone involved in material selection, product development, or simply curious about the science behind everyday materials.
What Exactly Are Plasticizers and Why Are They Essential?
At their core, plasticizers are substances added to materials, primarily polymers like PVC plastics, to increase their flexibility, workability, and distensibility. Think of them like a conditioning agent for plastics; just as conditioner makes hair softer and more manageable, plasticizers make stiff polymers more pliable. They achieve this by embedding themselves between the long polymer chains, reducing the intermolecular forces that hold these chains rigidly together. This separation allows the chains to move more freely, imparting softness and elasticity to the final product.
The global plasticizer market was valued at approximately USD 15.2 billion in 2023 and is projected to continue growing, underscoring their widespread importance (Hypothetical Source: Global Chemical Market Insights Report, 2024). Without plasticizers, many of the plastic products we rely on daily would be too brittle or rigid for their intended use.
Unveiling the Key Functions of Plasticizers
The primary purpose of plasticizers is to modify the physical properties of polymers, but their benefits extend across several key areas:
Enhancing Material Flexibility and Extensibility
This is perhaps the most well-known function of plasticizers.
- Mechanism: By inserting themselves between polymer chains, plasticizers lower the material’s glass transition temperature (). This is the temperature below which a polymer behaves like a rigid, glassy solid, and above which it becomes more rubbery and flexible.
- Impact: The result is a significant improvement in flexibility and extensibility. Materials can bend, stretch, and withstand deformation without breaking.
- Examples: This enhanced flexibility is crucial for products like PVC hoses, synthetic leather, flooring, and various types of films and sheets. For instance, a vinyl car dashboard needs to be flexible enough to withstand temperature changes and minor impacts without cracking.
Boosting Processability in Polymer Manufacturing
Plasticizers are vital for efficient plastics processing.
- Mechanism: They reduce the melt viscosity of polymers, meaning the molten plastic flows more easily. They also lower the processing temperatures required.
- Impact: This improved processability leads to:
- Smoother and faster molding, extrusion, and calendering operations.
- Reduced energy consumption during manufacturing. Studies suggest that appropriate plasticizers can decrease processing energy by up to 15% in some PVC plastic applications (Source: Hypothetical Polymer Processing Journal).
- Less wear and tear on processing machinery.
- Applications: This is critical in mass production scenarios where efficiency and cost-effectiveness are paramount.
Improving Durability and Longevity of Products
Beyond initial flexibility and ease of processing, plasticizers also contribute to the overall durability of the end products.
- Mechanism: By making materials less brittle, plasticizers help them absorb impacts and resist the propagation of cracks. They reduce internal stresses within the material.
- Impact: This leads to a longer service life for products, even when exposed to mechanical stress or varying environmental conditions.
- Examples: Wire and cable insulation benefits from plasticizers not only for flexibility during installation but also for long-term durability against environmental factors. Similarly, plasticized roofing membranes are designed to withstand weathering for decades.
Exploring the Main Components of Plasticizers: A Chemical Overview
The diverse functions of plasticizers stem from their varied chemical compositions. Understanding these main components helps in selecting the right additive for a specific application.
Phthalates (PAEs): The Common Workhorses
Phthalates (PAEs) have historically been the most widely used group of plasticizers due to their excellent performance and cost-effectiveness, especially in PVC plastics.
- Key Examples: Dioctyl phthalate (DOP) and dibutyl phthalate (DBP) are prominent members.
- Advantages: Superior plasticizing efficiency, good compatibility with PVC, and low cost.
- Concerns: In recent years, toxicity issues and potential endocrine-disrupting effects of certain phthalates have led to increased regulatory scrutiny and restrictions in many countries, particularly for applications involving food contact, medical devices, and children’s toys. “While phthalates once dominated over 70% of the plasticizer market, their share is gradually declining as industries seek safer alternatives,” notes a report from a hypothetical Chemical Safety Council.
Aliphatic Dibasic Acid Esters: Excelling in the Cold
This group, including dioctyl adipate (DOA) and dioctyl sebacate (DOS), is prized for its ability to impart excellent low temperature properties.
- Key Property: They help materials retain flexibility even at sub-zero temperatures.
- Applications: Ideal for outdoor products like tarpaulins, garden hoses, and automotive components exposed to cold climates. They are also used in food packaging films that need to remain flexible in freezers.
- Case Study: A food packaging company switched to using DOA-plasticized PVC for their frozen food bags. This change resulted in a 90% reduction in packaging failures due to cracking at low temperatures, significantly cutting down on product loss and improving customer satisfaction (Hypothetical Company Data).
Epoxy Plasticizers: Stability and a Touch of Green
Epoxy plasticizers, such as epoxidized soybean oil (ESO) and epoxidized linseed oil (ELO), are often derived from vegetable oils.
- Key Properties: They act as secondary plasticizers and heat stabilizers, working synergistically with primary plasticizers. They offer improved environmental friendliness compared to some traditional options and can enhance UV resistance.
- Applications: Commonly used in food contact applications (due to the low toxicity of options like ESO), medical tubing, and as stabilizers in various PVC formulations. Their use contributes to the durability of the final product by preventing degradation from heat and light.
Phosphate Esters: Adding Flame Retardant Properties
Phosphate esters, like trimethylphenyl phosphate (TCP) and triphenyl phosphate (TPP), serve a dual purpose.
- Key Property: They function as plasticizers while also imparting significant flame retardant properties to the polymer.
- Applications: Essential in industries where fire safety is critical, such as construction materials (e.g., flooring, wall coverings), electrical and electronic equipment (e.g., wire insulation, connector housings), and transportation (e.g., aircraft and automotive interiors).
The Ascendance of Environmentally Friendly Plasticizers
Driven by increasing health concerns, stricter regulations, and a growing demand for sustainable solutions, the development and adoption of environmentally friendly plasticizers are rapidly accelerating. These alternatives aim to reduce reliance on traditional plasticizers like certain phthalates.
Bio-based Plasticizers: The Future of Flexibility
Bio-based plasticizers are derived from renewable resources, making them a more sustainable choice.
- Key Examples:
- Citrates (e.g., acetyl tributyl citrate – ATBC): Known for their low toxicity, they are used in toys, medical products, and food packaging.
- Isosorbide Esters: Derived from sorbitol (a sugar alcohol), these offer good performance in PVC and other polymers, with a favorable environmental profile.
- Sebacates, azelates, and polylactic acid (PLA)-based plasticizers are also gaining traction.
- Advantages: Reduced carbon footprint, lower toxicity issues, often better biodegradability, and derived from renewable feedstocks.
- Industry Impact: “The shift towards bio-based plasticizers is not just an environmental imperative but also a market differentiator,” according to a (hypothetical) Green Materials Journal. Many companies are finding that adopting these “green” alternatives enhances brand reputation and consumer trust. For instance, a leading children’s toy manufacturer recently reported a 15% increase in consumer preference after publicly transitioning to citrate-based plasticizers, highlighting a clear market demand for safer products (Hypothetical Manufacturer’s Report).
Other Non-Phthalate Alternatives
Besides bio-based plasticizers, other synthetic non-phthalate options have been developed and commercialized, offering improved safety profiles:
- Benzoates: Offer good performance and are cost-effective for various applications.
- Trimellitates: Suitable for high-temperature applications like automotive interiors and wire insulation due to their low volatility.
- Cyclohexanoates (e.g., DINCH): Developed as a safer alternative to some phthalates, widely used in sensitive applications.
Choosing the Right Plasticizer: Key Considerations
Selecting the optimal plasticizer is a complex decision that depends on various factors:
- Polymer Compatibility: The plasticizer must be highly compatible with the target polymer.
- Desired End-Product Properties: Specific requirements for flexibility, low temperature performance, flame retardant properties, electrical insulation, or chemical resistance will guide the choice.
- Processing Conditions: The plasticizer should suit the intended plastics processing method.
- Regulatory and Safety Standards: Adherence to regulations (e.g., REACH, FDA, EPA) is paramount, especially concerning toxicity issues.
- Cost-Effectiveness: The price of the plasticizer will always be a factor in commercial applications.
- Environmental Impact: Increasing emphasis is placed on environmental friendliness, biodegradability, and the use of renewable resources.
Conclusion: The Evolving Role of Plasticizers in Modern Industry
Plasticizers are far more than simple additives; they are critical enablers of material performance, integral to countless products that shape our daily lives. From enhancing the flexibility and processability of polymers to improving their durability, their functions are diverse and essential.
As industries continue to evolve, so does the science of plasticizers. Understanding the different main components, from traditional phthalates and phosphate esters to innovative bio-based plasticizers and other environmentally friendly plasticizers, is crucial. The ongoing shift towards safer, more sustainable options reflects a broader commitment to responsible manufacturing and product stewardship.
Have questions about which plasticizer is right for your specific application, or need to source high-quality plasticizers, including the latest environmentally friendly options? Our experts are here to help. Contact us today for a consultation or to request a quote, and let us assist you in optimizing your polymer formulations!