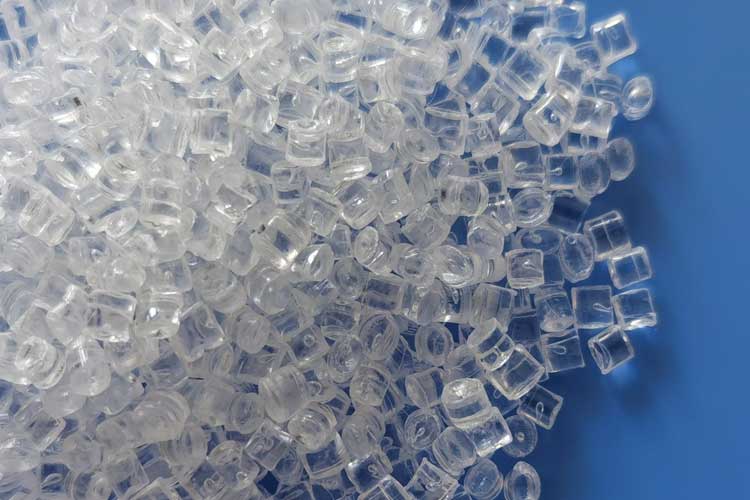
Guarding Against the Sun: The Crucial Role of Light Stabilizers for Polymer Materials
Every day, the polymer materials that make up countless products – from car bumpers and outdoor furniture to vibrant coatings and durable agricultural films – face a relentless adversary: sunlight. The UV radiation component of sunlight, while invisible to us, is a powerful force that can trigger photooxidative degradation, leading to cracking, discoloration, and a dramatic loss of structural integrity. But what if we could give these materials an invisible shield? This is precisely where Light Stabilizers come into play. These remarkable additives are the unsung heroes in the world of polymer materials, working diligently to inhibit or slow down the damaging effects of light.
As the use of synthetic polymers continues to expand, especially in applications demanding outdoor durability, the importance of light stabilizers has grown exponentially. They are now an indispensable category of plastic additives. This article will delve into the science behind light stabilizers, exploring their mechanism of action, the different type breakdown, key ingredients, crucial performance considerations, and their ultimate application goals in extending material life and providing essential UV protection.
If you’re searching for specific light stabilizer products, CAS numbers, or need expert advice for your polymer formulations, you’re in the right place. Our team is dedicated to helping you find the optimal solution.
The Enemy Within: Understanding Photooxidative Degradation in Polymer Materials
Before we explore the solutions, let’s understand the problem. When polymer materials like plastics, coatings, rubber, chemical fibers, and adhesives are exposed to UV radiation, a destructive chain of events known as photooxidative degradation can be initiated.
Here’s a simplified look at this process:
- Activation: UV photons possess enough energy to break chemical bonds within the polymer structure or excite sensitizing impurities (chromophores) present in the material.
- Free Radical Formation: This bond-breaking or energy transfer leads to the formation of highly reactive free radicals.
- Propagation: These initial free radicals react with oxygen (which is almost always present) to form peroxy radicals. Peroxy radicals can then abstract hydrogen atoms from other polymer chains, creating new alkyl radicals and hydroperoxides. This sets off a damaging chain reaction.
- Degradation: Hydroperoxides are unstable and can decompose, especially under heat or further UV exposure, forming more radicals and leading to chain scission (breaking of the polymer backbone) or cross-linking.
The visible consequences of photooxidative degradation are all too common:
- Loss of gloss and surface chalking in coatings.
- Yellowing or other discoloration.
- Embrittlement, leading to cracks and fractures.
- Reduction in tensile strength, impact resistance, and elasticity.
- Overall shortened service life of the product.
Without protection, many polymer materials would fail prematurely when used outdoors or exposed to artificial UV sources. For instance, unprotected polypropylene can show significant degradation within months of outdoor exposure in sunny climates.
The Guardians Arrive: What Are Light Stabilizers?
Light stabilizers are specialized chemical additives incorporated into polymer materials during manufacturing to interfere with the photooxidative degradation process. Their primary application goal is to significantly enhance the durability and extend the material life of polymers by providing robust UV protection. They don’t make the polymer invincible, but they dramatically slow down the rate at which light-induced damage occurs.
Think of them as a sophisticated defense system. Some act like sunscreens, others like medics, and some like bodyguards, all working to keep the polymer structure intact for longer. The global market for light stabilizers is a multi-billion dollar industry, underscoring their critical importance across numerous sectors.
Unmasking the Protectors: The Four Main Types of Light Stabilizers
Light stabilizers achieve their protective effects through various mechanisms. They are broadly categorized into four main types:
1. Free Radical Scavengers: The Vigilant Hindered Amine Light Stabilizers (HALS)
This class, predominantly featuring Hindered Amine Light Stabilizers (HALS), is one of the most effective and widely used for long-term UV protection.
- Mechanism of Action: HALS don’t primarily absorb UV radiation. Instead, their genius lies in their ability to scavenge or “trap” the free radicals that are formed during the initial stages of photooxidative degradation. The hindered amine functional groups (typically cyclic aliphatic amines) in HALS are converted into stable nitroxide free radicals (NO•) in the presence of oxygen and light energy. These nitroxyl radicals are highly efficient at reacting with and deactivating the detrimental alkyl and peroxy radicals in the polymer.
- The Regenerative Cycle: A key advantage of HALS is their regenerative nature. After deactivating a polymer radical, the HALS derivative can be reformed, allowing a single HALS molecule to neutralize many free radicals during its lifetime. This “catalytic” scavenging cycle makes them extremely efficient even at relatively low concentrations.
- Key Ingredients/Examples: Popular HALS include products commonly designated by numbers such as 770 (Tinuvin 770), 622 (Tinuvin 622), 944 (Chimassorb 944), 783 (a synergistic blend), and 2020.
- Benefits: HALS are effective in thick sections, offer excellent long-term thermal stability and light stability, and are compatible with a wide range of polymer materials. They are particularly effective in polyolefins (polyethylene, polypropylene), styrenics, and polyamides.
2. UV Absorbers (UVAs): The First Line of Defense
UV Absorbers (UVAs) function much like sunscreen for polymers.
- Mechanism of Action: They absorb harmful UV radiation and convert it into harmless thermal energy, which is then dissipated throughout the polymer matrix. This prevents the UV photons from reaching the polymer chains and initiating degradation.
- Type Breakdown & Key Ingredients:
- Benzophenones: These are broad-spectrum UV absorbers, effective against UV-A, UV-B, and even some UV-C radiation. A common example is UV-531 (2-hydroxy-4-n-octoxybenzophenone). Their mechanism of action involves an intramolecular hydrogen bond that, upon UV absorption, facilitates a molecular rearrangement (enol-keto tautomerism), allowing the energy to be released as heat.
- Benzotriazoles: These are highly effective UVAs known for their strong absorption in the UV-B and UV-A regions. They offer excellent photostability and are often used in coatings, polycarbonates, and polyesters where clarity is important.
- Triazines (Hydroxyphenyltriazines – HPTs): This newer class of UVAs offers very high performance, excellent photostability, and low volatility, making them suitable for demanding applications and long-term outdoor exposure in materials like polyamides, polycarbonates, and high-performance coatings.
- Salicylates: Historically important, salicylates (like phenyl salicylate) are milder UV absorbers. They undergo a photo-Fries rearrangement to form dihydroxybenzophenone derivatives, which are themselves UV absorbing. They are less common now but can be found in some specific applications.
- Effectiveness: UVAs are most effective at protecting the surface layers of a material or thin articles.
3. Quenchers: Deactivating Excited States
These stabilizers operate by deactivating excited state molecules within the polymer.
- Mechanism of Action: When polymer molecules or impurities (chromophores) absorb UV energy, they can enter an “excited state.” If not deactivated, these excited molecules can transfer their energy to oxygen to form singlet oxygen (a highly reactive species) or decompose directly, initiating degradation. Quenchers intercept this energy from the excited chromophore and dissipate it harmlessly, often as heat, returning the chromophore to its ground state.
- Key Ingredients: Metal complexes, particularly organic complexes of nickel, cobalt, or iron, are common quenchers. Some HALS also exhibit a quenching effect in addition to their primary free-radical scavenging mechanism.
- Application: They are often used in agricultural films and synthetic fibers, sometimes in synergy with UV absorbers.
4. Light Shielding Agents (Opaquants): The Physical Barrier
These create a physical barrier to UV light.
- Mechanism of Action: Light shielding agents protect polymer materials by either reflecting or absorbing UV radiation, thereby preventing it from penetrating into the bulk of the material. They essentially make the material opaque to UV light.
- Key Ingredients:
- Carbon Black: An exceptionally effective light screener. It absorbs UV radiation across a broad spectrum and converts it to heat. Even at low loadings (e.g., 2-3%), carbon black can provide outstanding UV protection, making it a top choice for applications like black polyethylene pipes and cables designed for decades of outdoor service.
- Titanium Dioxide (TiO₂): Primarily a white pigment, titanium dioxide (especially the rutile form) also effectively scatters and reflects UV radiation, offering good protection. It’s widely used in PVC window profiles, sidings, and white coatings.
- Zinc Oxide (ZnO): Another white pigment that provides UV shielding. It can also offer some antimicrobial benefits.
- Other Opaque Pigments: Materials like zinc barium sulfate (lithopone) can also contribute to light shielding.
- Consideration: While highly effective, these agents also impart color or opacity to the material, so they are not suitable for applications requiring transparency or specific colors other than what the shielding agent provides.
Choosing Your Champion: Key Performance Considerations for Light Stabilizers
Selecting the right light stabilizer, or combination of stabilizers, is a complex decision that goes beyond just their primary function. Several performance considerations must be taken into account:
-
Compatibility with the Polymer: This is paramount. The light stabilizer must be adequately soluble or dispersible in the polymer material at processing and end-use temperatures. Poor compatibility can lead to issues like:
- Exudation (blooming) to the surface, causing tackiness, loss of protection, and aesthetic defects.
- Reduced efficiency of the stabilizer.
- Opacity or haze in clear applications.
- A Note: Since light stabilizers are often used at higher concentrations (sometimes 0.5% to 1% or even more by weight) compared to other additives like antioxidants, their compatibility is even more critical.
-
Thermal Stability: The stabilizer must withstand the high temperatures encountered during polymer processing (e.g., extrusion, injection molding) without decomposing or losing its effectiveness.
-
Volatility: Low volatility is crucial. A volatile stabilizer can be lost during processing or evaporate from the finished product over time, especially at elevated service temperatures, leading to a premature reduction in UV protection.
-
Physical Form, Particle Size, and Distribution: Light stabilizers come in various forms (powders, granules, liquids). Their physical form, particle size, and ability to distribute uniformly within the polymer matrix are important for handling ease and consistent performance.
-
Interactions with Other Additives: Polymers rarely contain just one additive. Light stabilizers must be compatible with other components like antioxidants, pigments, fillers, flame retardants, etc. Some interactions can be synergistic (beneficial), while others can be antagonistic (detrimental). For example, some acidic substances can impair the performance of certain HALS.
-
Toxicity and Regulatory Compliance: For applications involving food contact, medical devices, toys, or personal care products, the light stabilizer must meet stringent regulatory requirements (e.g., FDA, EFSA approvals) and have a low toxicity profile.
-
Color and Transparency: The stabilizer should not impart undesirable color or haze, especially in applications requiring high clarity or specific color matching (unless it’s a light shielding agent like carbon black or titanium dioxide intended for that purpose).
-
Extraction Resistance: In applications where the polymer comes into contact with liquids (e.g., water, solvents, detergents), the stabilizer should resist extraction to maintain long-term protection.
-
Cost-Effectiveness: The chosen light stabilization system must provide the desired level of UV protection for the intended service life of the product at an acceptable cost.
Often, achieving optimal UV protection involves using a synergistic blend of light stabilizers, such as a UVA combined with a HALS. The UVA provides surface protection by absorbing UV light, while the HALS scavenges free radicals throughout the bulk of the material. This combination can be far more effective than using either type alone. Industry data suggests that well-chosen stabilizer packages can extend the useful life of polymer materials in outdoor applications by 3 to 10 times, or even more, depending on the severity of UV exposure and the polymer type.
Real-World Impact: Case Studies of Light Stabilizers in Polymer Materials
Case Study 1: Automotive Exterior Parts
- Challenge: An automotive manufacturer was experiencing premature color fading and surface cracking on polypropylene (PP) exterior trim parts exposed to intense sunlight and varying temperatures.
- Solution: They worked with an additive supplier to incorporate a synergistic blend of a high-performance benzotriazole UV absorber and a non-basic HALS into their PP compound.
- Outcome: The stabilized PP parts exhibited significantly improved color retention (e.g., a 75% reduction in color shift after 2000 hours of Xenon arc weathering testing) and maintained their mechanical integrity well beyond the warranty period, enhancing vehicle aesthetics and customer satisfaction. This resulted in a measurable decrease in warranty claims related to UV degradation.
Case Study 2: Agricultural Greenhouse Films
- Challenge: A producer of polyethylene (PE) greenhouse films needed to extend the service life of their films from one growing season to at least three, particularly in regions with high UV intensity, to offer better value to farmers.
- Solution: They adopted a specialized HALS formulation designed for agricultural applications, which also offered good resistance to agrochemicals. Consideration was also given to key ingredients like metal complexes (quenchers) to supplement protection.
- Outcome: The new greenhouse film demonstrated enhanced durability, lasting for 3-4 seasons. This not only saved farmers replacement costs but also contributed to more consistent crop yields due to stable light transmission properties of the film over a longer period.
Case Study 3: Durable Outdoor Coatings
- Challenge: A paint manufacturer’s acrylic-based exterior coating for architectural applications was showing early signs of chalking (formation of a powdery surface) and gloss reduction in sunny, humid climates.
- Solution: The coating was reformulated to include a high-performance triazine-based UVA for strong surface protection and a low-volatility HALS to protect the bulk of the coating film. The thermal stability of these additives was also critical during the paint curing process.
- Outcome: The reformulated coating showed a marked improvement in gloss retention and resistance to chalking, extending the maintenance cycle for painted structures and improving the coating’s overall UV protection and aesthetic appeal.
The Future of Light Stabilization: Greener and Smarter Solutions
The field of light stabilizers is continuously evolving. Current research and development efforts are focused on:
- Higher Efficiency: Creating stabilizers that offer superior protection at even lower concentrations.
- Enhanced Durability & Persistence: Developing stabilizers with better thermal stability, lower volatility, and greater resistance to extraction for very long-term applications.
- Improved Compatibility: Designing stabilizers that are more easily incorporated and more compatible with a wider range of existing and emerging polymer materials, including bioplastics and recycled polymers.
- Sustainability: A strong push towards “greener” light stabilizers with more favorable environmental profiles, reduced migration potential, and derived from renewable resources.
- Intelligent Stabilization: Exploring systems that can adapt to changing environmental stresses or indicate when the polymer is nearing the end of its stabilized life.
Regulations also continue to shape the market, driving demand for safer and more environmentally sound solutions without compromising on the application goals of performance and durability.
Conclusion: Securing Longevity for Polymer Materials
Light stabilizers are indispensable guardians of polymer materials, playing a vital role in protecting them from the damaging effects of UV radiation and photooxidative degradation. By understanding the diverse type breakdown—from radical-scavenging HALS and UV-absorbing benzophenones to energy-quenching metal complexes and barrier-forming light shielding agents like carbon black and titanium dioxide—manufacturers can make informed choices.
Careful consideration of performance considerations such as compatibility, thermal stability, and volatility ensures that these additives deliver on their promise of extending material life and maintaining aesthetic and functional properties. As technology advances, we can expect even more sophisticated and sustainable light stabilization solutions to emerge, further enhancing the durability and utility of the polymer materials that shape our world.
Are you facing challenges with UV degradation in your polymer products? Looking for the ideal light stabilizer system, specific product grades, or CAS numbers to enhance performance and longevity?
Our team of experts specializes in light stabilization technology for a wide array of polymer materials. We are here to provide technical support, product recommendations, and customized solutions to meet your specific needs. Don’t let the sun compromise your product’s integrity. Contact us today for a consultation and let us help you safeguard your materials for a brighter, longer-lasting future!