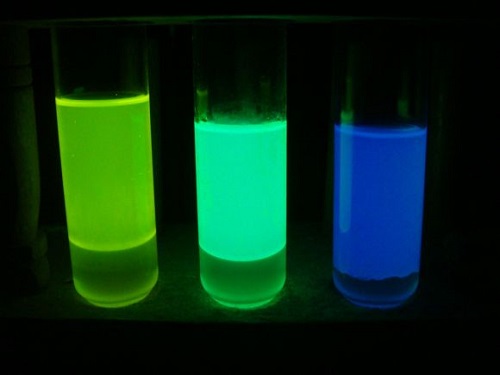
Unveiling the Brilliance: Understanding Fluorescent Whitening Agents and Their Whitening Principle
Ever wondered how your white textiles maintain their dazzling brightness, or how paper products achieve that crisp, clean look? The secret often lies in a fascinating class of organic compounds known as Fluorescent Whitening Agents (FWAs), also sometimes called optical brighteners or fluorescent brightening agents (FBAs). These are not your typical dyes; instead of imparting color, they work through a unique optical mechanism to make materials appear whiter and brighter. This article delves into the core of Fluorescent Whitening Agent (FWA) technology and its whitening principle, exploring their properties, classifications, application factors, and how to achieve the best results.
If you’re looking for specific FWA products, CAS numbers, or expert advice on their application, you’ve come to the right place. Our team is ready to assist you with your specific needs!
What Exactly Are Fluorescent Whitening Agents? The Chemical Perspective
Fluorescent Whitening Agents are essentially colorless to pale-colored fluorescent dyes. Chemically, they are complex organic compounds designed with a special characteristic: they absorb light in the invisible ultraviolet (UV) and violet region of the electromagnetic spectrum (typically 300-400 nm) and re-emit it as blue-violet light (typically 420-480 nm) in the visible spectrum. This phenomenon is known as fluorescence.
The key features of FWAs include:
- Selective Absorption: They absorb UV light, which is invisible to the human eye.
- Light Re-emission: They convert this UV energy into visible blue light.
- Optical Effect: This emitted blue light counteracts any natural yellowish tint in materials, making them appear whiter and brighter.
It’s crucial to understand that the whitening effect of FWAs is an optical whitening phenomenon – an illusion of sorts. They don’t chemically bleach the material to remove color or stains. Instead, they add blue light, which our eyes perceive as increased whiteness. Think of it like a subtle “blue rinse” for fabrics, but achieved through light manipulation!
The Core Concept: The Whitening Principle of FWAs Explained
The whitening principle behind Fluorescent Whitening Agents is a fascinating interplay of light absorption and emission. Here’s a step-by-step breakdown:
- UV Absorption: When an FWA-treated material is exposed to a light source containing UV rays (like sunlight or some artificial lights), the FWA molecules absorb this high-energy UV light.
- Molecular Excitation: This absorption of energy causes the electrons within the FWA molecules to jump to a higher energy state (an excited state).
- Energy Release & Fluorescence: The excited state is unstable. As the electrons return to their original, lower energy state (ground state), they release the excess energy. Part of this energy is lost as heat, but a significant portion is emitted as visible light.
- Blue-Violet Light Emission: Crucially, the emitted light has a longer wavelength and lower energy than the absorbed UV light. This emitted light falls predominantly in the blue to blue-violet part of the visible spectrum (around 420-480 nm).
- Optical Compensation: Many materials, especially natural fibers like cotton or even processed materials like paper and plastics, tend to absorb blue light and reflect yellow light, giving them a slightly yellowish or dull appearance. The blue-violet light emitted by the FWA compensates for this yellowish tinge. By adding blue light to the light reflected from the material, the overall perceived color shifts towards white, making the material appear brighter and cleaner.
This optical whitening is purely additive. FWAs don’t remove the yellow; they mask it by adding its complementary color, blue. This is why FWAs are sometimes referred to as providing an “optical bleach” effect, though it’s important to remember this is distinct from chemical bleaching, which chemically alters stain molecules or inherent color.
Diverse Chemistries: Classification of Fluorescent Whitening Agents
FWAs are not a one-size-fits-all solution. Their chemical structures are diverse, allowing for tailored applications across various materials and industries. They are broadly classified based on their parent chemical structure. While there are many categories, here are some of the most significant ones:
- Triazinylaminostilbene Derivatives: This is arguably the most important and widely used class, constituting a significant majority (reportedly over 80%) of all commercially produced FWAs. These compounds are derived from 4,4′-diamino-stilbene-2,2′-disulfonic acid (DSD acid) and cyanuric chloride. They are valued for their effectiveness on cellulosic fibers (cotton, linen, rayon), paper, and detergents.
- Benzoxazoles: This group represents the second-largest class in terms of production volume. Benzoxazoles are often high-performance FWAs known for their good light fastness and stability. They find applications in plastics (like PVC, polystyrene, polyolefins), synthetic fibers (polyester, nylon), and sometimes in detergents. A typical example is Eastobrite OB-1, widely used for polyester fibers and plastics.
- Stilbene-Triazoles: These were among the earlier types of FWAs. However, their tendency to produce a greenish tint and achieve relatively lower whiteness levels on fibers has led to their decline in the market.
- Carbon-Cyclic Types: These FWAs have a molecular structure that does not contain heterocyclic rings in their core or substituents. Key parent molecules include 1,4-Distyrylbenzene, 4,4’-Distyrylbiphenyl, and 4,4’-Divinylstilbene. Cyano-substituted distyrylbenzenes, for example, exhibit high fluorescence quantum yields and are particularly effective for plastics and synthetic fiber resins. Palanil Brilliant White R is a representative product.
- Furan, Benzofuran, and Benzimidazole Derivatives: While these heterocyclic systems themselves might not be the FWA parent, they are crucial structural units. When combined with other units like biphenyl, they can form highly effective FWAs. Sulfonated versions of these compounds offer good water solubility, making them suitable for nylon and cellulosic fibers.
- Coumarins: Coumarin itself exhibits strong fluorescence. By introducing various substituent groups at specific positions (e.g., 4- and 7-positions), derivatives with practical value as FWAs can be created. They are used in soaps, detergents, and plastics.
- Other Classes: Naphthalimides and 1,3-diphenyl-2-pyrazolines are other notable classes, each with specific properties and application areas.
The choice of FWA depends heavily on the substrate to be whitened, the desired level of whiteness, processing conditions, and cost-effectiveness.
Maximizing Brilliance: Key Factors Influencing FWA Performance
Achieving the optimal whitening effect with FWAs isn’t just about applying them; several factors can significantly influence their performance:
- Substrate Pre-treatment & Initial Whiteness: The cleaner and whiter the base material, the better the FWA will perform. If a material is heavily soiled or very yellow, FWAs alone might not achieve the desired brightness. Chemical bleaching may be necessary as a pre-treatment.
- FWA Concentration (The “Yellowing Point”): There’s an optimal concentration for every FWA on a given substrate. Initially, as FWA concentration increases, whiteness improves. However, exceeding a certain limit, known as the saturation concentration or “yellowing point,” can lead to a decrease in whiteness and even a “greening” or “pinking” hue, or a dull, yellowing appearance. This is because excessive FWA can lead to self-absorption of the emitted fluorescence or an over-compensation of blue light.
- Example Yellowing Points:
- FWA DT (for polyester): ~0.08%
- FWA VBL (for cotton): ~0.5%
- FWA DCB (for acrylic): ~0.8%
- FWA CH (for acrylic bulked yarn): ~3.3%
- Example Yellowing Points:
- pH Value: The pH of the application medium (e.g., dye bath) is critical. Different FWAs have different optimal pH ranges.
- Anionic FWAs (common for cotton) often perform best in neutral to slightly alkaline conditions and may lose effectiveness or stability in highly acidic environments.
- Cationic FWAs may see a drop in absorbance if the pH becomes too high (e.g., pH > 9). The pH can affect the FWA’s solubility, stability, and its affinity for the fiber.
- Surfactants: The presence of surfactants can impact FWA performance, especially for ionic FWAs.
- Surfactants with an opposite charge to the FWA can reduce its effectiveness or even cause fluorescence quenching (loss of fluorescence).
- Surfactants with the same charge, or non-ionic surfactants, generally have minimal to no adverse effect and can sometimes aid in dispersion or leveling.
- Inorganic Salt Effects: In some FWA applications, particularly in dyeing processes for textiles, inorganic salts like sodium chloride (NaCl) or sodium sulfate (Na₂SO₄) are added. These salts can increase the FWA’s exhaustion rate (the amount that transfers from the bath to the fiber) by reducing its solubility in water and decreasing the electrostatic repulsion between anionic FWAs and negatively charged fibers like cotton.
- Water Quality: The presence of impurities in water, such as heavy metal ions (iron, copper) or high hardness, can negatively affect FWA performance. These ions can form complexes with FWAs, reducing their fluorescence or causing discoloration. Using soft water is generally recommended.
- Presence of Other Chemicals & Color Light Adjustment: When FWAs are used alongside other finishing agents, dyes, or auxiliaries, their interactions can slightly alter the final shade. Sometimes, minute quantities of specific dyes are used for color light adjustment to achieve a precise desired hue of white (e.g., a slightly reddish-blue white or a greenish-blue white).
- Light Source: Since FWAs rely on UV light for activation, the perceived whiteness can vary under different lighting conditions. Materials may appear brighter in daylight (rich in UV) than under incandescent light (low in UV).
Understanding these factors is crucial for formulators and manufacturers to optimize the use of FWAs and achieve consistent, high-quality results.
Common Problems and Solutions in FWA Application
While highly effective, FWAs can present challenges if not used correctly.
Problem 1: Whiteness Reduction at High Concentrations
As mentioned, using too much FWA can decrease whiteness. Why does this happen?
- Limited Yellow to Counteract: The amount of inherent yellowness in a fabric is finite. Once enough blue-violet light is emitted to neutralize this yellowness, additional blue-violet light can make the fabric appear overtly blue or even grayish, reducing the perceived “true” whiteness.
- Optical vs. Chemical: FWAs only provide an optical whitening effect. They don’t replace the need for proper chemical bleaching to remove underlying stains or discoloration on heavily soiled or unbleached materials.
- Over-Compensation: If the FWA concentration is too high, the intensity of the emitted blue-violet light can overwhelm the yellow light it’s meant to counteract. This imbalance shifts the perceived color, often leading to a less desirable shade.
- Self-Quenching/Aggregation: At very high concentrations, FWA molecules can interact with each other in ways that reduce their overall fluorescence efficiency (e.g., through aggregation or self-quenching).
Problem 2: The Dreaded “Yellowing Point” and General Yellowing
The yellowing point refers to the FWA concentration beyond which whiteness begins to decrease and an undesirable tint appears. General yellowing of FWA-treated materials can also occur over time due to:
- Atmospheric Contaminants: Exposure to acidic gases (like oxides of nitrogen or sulfur dioxide) or chlorine in the atmosphere, especially in humid conditions, can degrade some FWAs or affect the fabric, leading to yellowing.
- Improper Processing: Residual alkali or acid from scouring and bleaching processes, if not thoroughly neutralized and rinsed, can affect FWA stability and lead to yellowing.
- Incompatible Softeners: Cationic softeners or certain silicone-based softeners can sometimes cause yellowing on white fabrics treated with anionic FWAs due to interactions.
- Water Impurities: As mentioned, heavy metal ions in process water can contribute to dullness or yellowing.
Solutions for Optimal FWA Performance:
- Control Dosage: Strictly adhere to recommended FWA concentrations. Conduct trials to determine the optimal yellowing point for your specific FWA, substrate, and process.
- Thorough Preparation & Rinsing: Ensure proper scouring and bleaching processes. Thoroughly rinse and neutralize materials after chemical treatments (e.g., after mercerization or bleaching) to remove residual chemicals. Consider using effective neutralizing agents like acetic acid or specialized neutralizers that can penetrate the fiber core, especially for heavier fabrics.
- pH Control: Maintain the optimal pH range for the FWA being used throughout the application process. Using soft water and maintaining a slightly alkaline pH (e.g., pH 8-9) is often beneficial for common anionic FWAs on cellulose.
- Select Compatible Auxiliaries: Choose softeners and other finishing agents that are compatible with your FWA. Anionic softeners are generally a safer choice for white goods treated with anionic FWAs.
- Water Quality Management: Use soft water with low levels of heavy metal ions for FWA application.
- Storage Conditions: Protect treated materials from exposure to atmospheric pollutants like acidic gases or excessive chlorine, especially in high humidity.
- Choose Robust FWAs: Select FWAs with good stability against acid, alkali, chlorine, and light, appropriate for the intended application and end-use of the material.
Case Studies: FWAs in Action
Case Study 1: Enhancing Cotton Textile Whiteness
A textile mill specializing in high-quality cotton bed linens was aiming to achieve a superior, lasting whiteness.
- Challenge: Achieving consistent, brilliant white that didn’t yellow after washing and stood out in the market.
- Solution: They transitioned to a high-affinity triazinylaminostilbene FWA known for its excellent performance on cellulosic fibers. Key steps included:
- Optimizing their bleaching process to achieve a high base whiteness.
- Careful control of FWA dosage, ensuring it was below the yellowing point.
- Maintaining a consistent pH of 8.5 in the application bath.
- Using an anionic softener compatible with the FWA.
- Result: The mill achieved a noticeable improvement in the brilliance and perceived quality of their linens, leading to positive customer feedback and a 15% increase in sales for their premium white collection within a year (hypothetical statistic for illustration).
Case Study 2: Brightening Recycled Plastics
A plastics manufacturer using recycled PET for packaging faced issues with the inherent yellowish tint of the recycled material.
- Challenge: Making the recycled plastic visually appealing and comparable to virgin material without significantly increasing costs.
- Solution: They incorporated a benzoxazole-type FWA (like Eastobrite OB-1) into their extrusion process. This FWA was chosen for its heat stability and effectiveness in polyesters.
- Dosage was carefully calibrated during compounding.
- Processing temperatures were monitored to ensure FWA stability.
- Result: The FWA successfully masked the yellowish tint, significantly improving the aesthetic quality of the recycled PET packaging. This allowed them to market their products as both sustainable and visually premium, opening up new market segments. Independent consumer panels rated the FWA-treated recycled plastic as 25% more appealing than the untreated version (hypothetical statistic).
The Future of Whiteness: Innovations and Considerations
Research in FWAs continues, focusing on:
- Higher Efficiency: Developing FWAs that provide greater whitening with lower concentrations.
- Improved Stability: Enhancing resistance to light, heat, chemicals, and laundering.
- Environmental Profile: Creating more biodegradable FWAs with lower environmental impact.
- Specific Applications: Tailoring FWAs for new materials and advanced technological applications.
While FWAs are invaluable, considerations regarding their environmental fate and potential for skin sensitization (though rare and typically associated with specific older types or high concentrations) are ongoing topics of research and regulation in some regions. Reputable manufacturers adhere to safety guidelines and provide data on their products.
Conclusion: Harnessing the Power of Light with Fluorescent Whitening Agents
Fluorescent Whitening Agents are remarkable organic compounds that leverage the optical mechanism of fluorescence to transform how we perceive whiteness. By understanding the whitening principle—ultraviolet absorption and blue-violet light emission—and carefully managing application factors like pH value, dosage (avoiding saturation concentration and yellowing points), and interactions with surfactants and inorganic salts, industries can achieve brilliant, appealing products.
From the brightest textiles to the crispest papers and vibrant plastics, FWAs play a subtle yet crucial role. They demonstrate how a deep understanding of light and chemistry can lead to significant enhancements in material quality and consumer appeal.
Do you have questions about selecting the right Fluorescent Whitening Agent for your specific application? Are you looking for a particular FWA by name or CAS number?
Our team of experts is here to help. We can provide technical data, product recommendations, and guidance to help you achieve the optimal whitening results. Contact us today to discuss your needs and let us illuminate the path to brighter products!